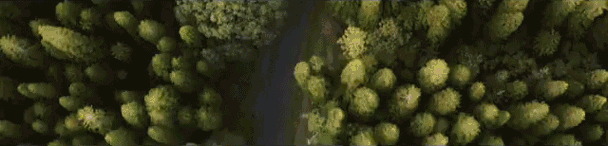
近日,在ATC新能源动力系统技术周上,纬湃科技中国电气化解决方案事业群创新部总监李智文介绍了嵌入式功率模块,指出印刷电路板(PCB)嵌入功率芯片技术的极大性能潜力,并对这一封装技术做出前景展望。
以下文字稿整理于《PCB嵌入式功率模块技术走势分析和应用前景》主题演讲。
新能源汽车主驱逆变器的功率模块传统上以框架式模块和注塑式为代表,作为主要封装形式。这两种封装都使用了高导热和电气绝缘的覆铜陶瓷基板作为功率芯片的载体,在功率传导和芯片散热中起到重要的作用。
但是,布置于陶瓷基板上的功率芯片在电气连接上只能通过陶瓷表面覆铜进行单层布线,辅以架空键合线等方式完成完整的功率电路连接。这种连接方式使得电气性能和散热受到了很大的限制,特别是降低换流回路和栅极控制回路的杂感和芯片间的热耦合方面。
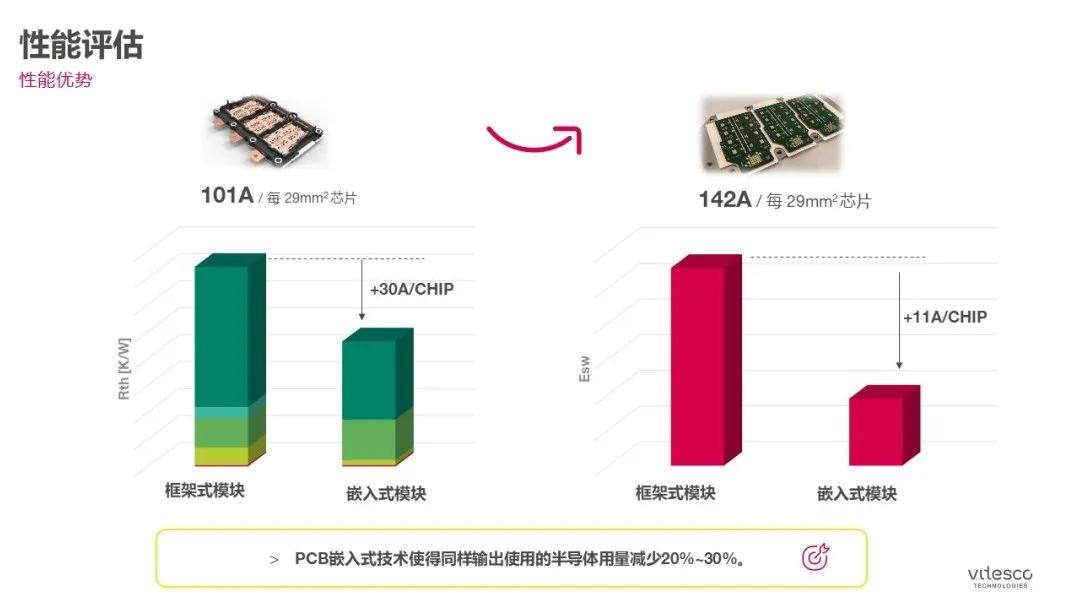
印刷电路板(PCB)天然具有以下优异的电气性能:PCB可以进行多层布线,通过控制线间距及层间距减少EMC的影响,绝缘材料可以满足400~1000V高压绝缘的要求,并且埋入PCB的电子器件可以通过高散热材料和合理的散热层设计达到优秀的散热性能。这些性能优势使得PCB嵌入功率芯片技术用于功率模块封装设计具有极大的性能潜力。
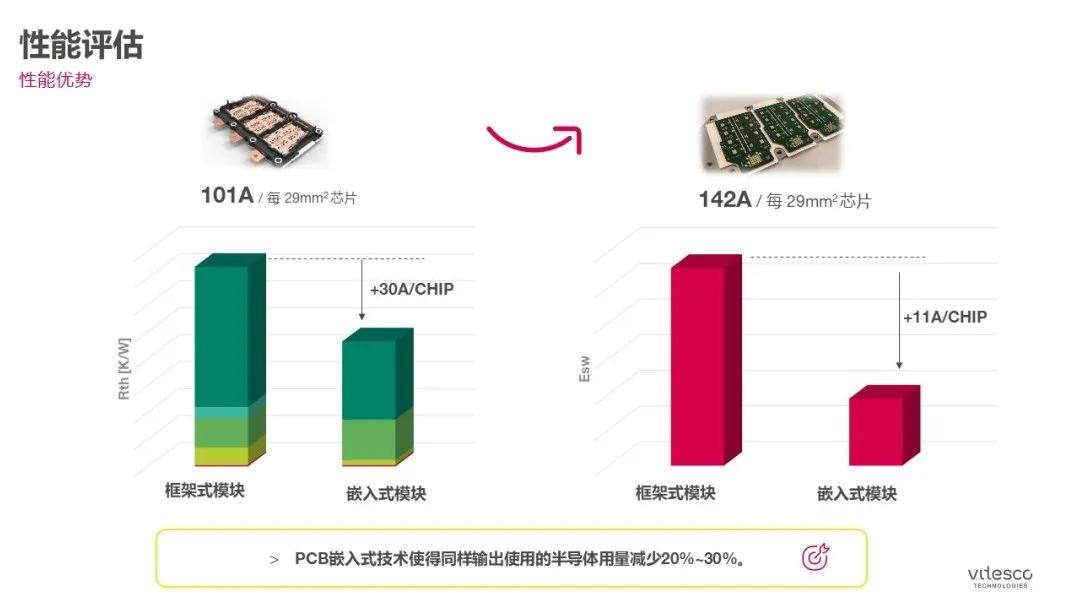
通过技术评估,我们认为相较于传统封装形式,PCB嵌入式功率模块单位半导体的通流能力可以提升约40%,或者同样电流输出使用的半导体用量减少1/3。同样功率输出条件下,功率模块物料成本有望降低20%。
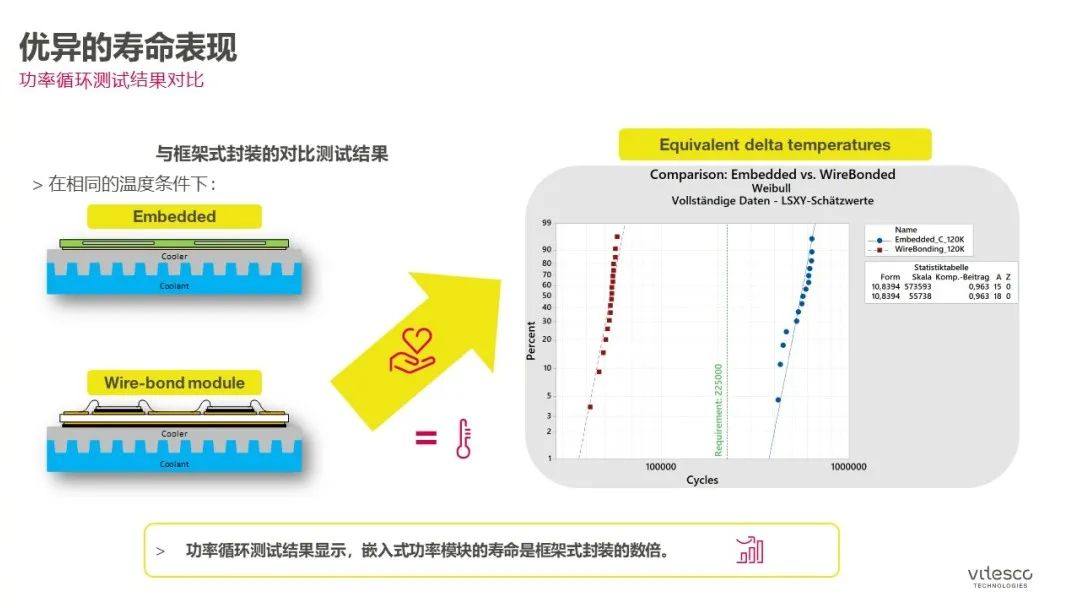
由于新型封装的功率换流回路杂感可降低到1nH以下,使得逆变器的整体开关损耗降低到原有逆变器产品的1/3,从而开关频率的提升所带来的开关损耗的增加相对于传统逆变器降低了2/3。
整车上可以通过提高开关频率来提升电驱系统整体的效率,从而基于同样的续航里程减少了电池的用量,最终达到整车降本的目的。同时更高的开关频率使得更小的逆变器体积,以及同样极对数下控制更高速的电机成为可能。
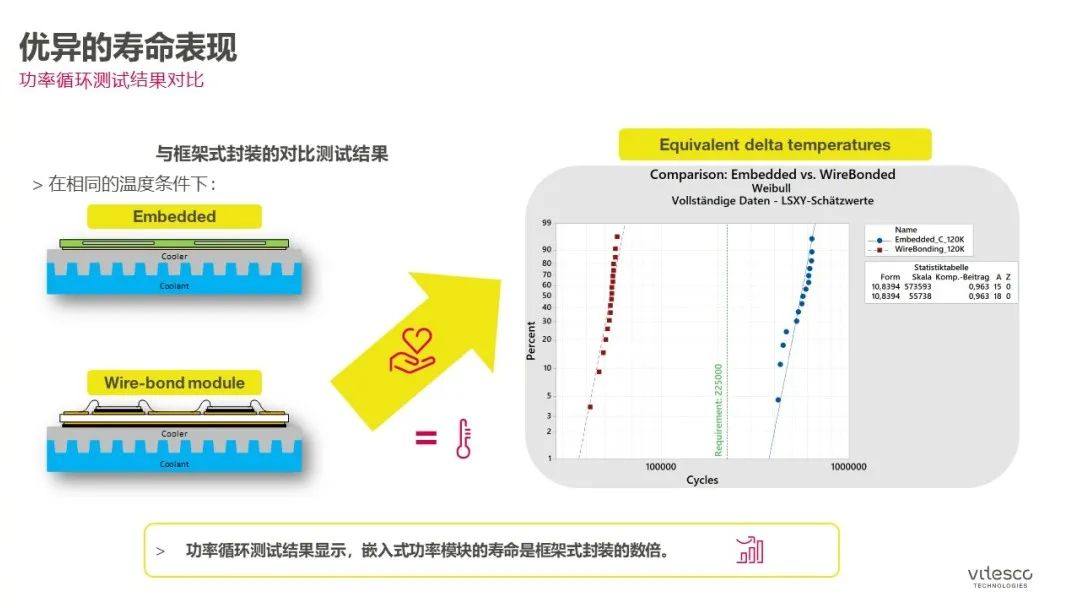
基于目前样品进行的AQG324关键可靠性验证表明,PCB嵌入式封装的设计寿命可达传统封装的数倍。
基于这一结果,纬湃科技做了一定的探索,测试PCB材料对功率芯片的高工作结温的耐受,PCB对不同工况下的温度变化的耐受,以及PCB工作在高电压大电流工况下的绝缘性能等。纬湃科技发挥多年来在传统封装设计中积累的经验,攻克多种技术挑战,最终将完成PCB嵌入式功率模块的产业化。
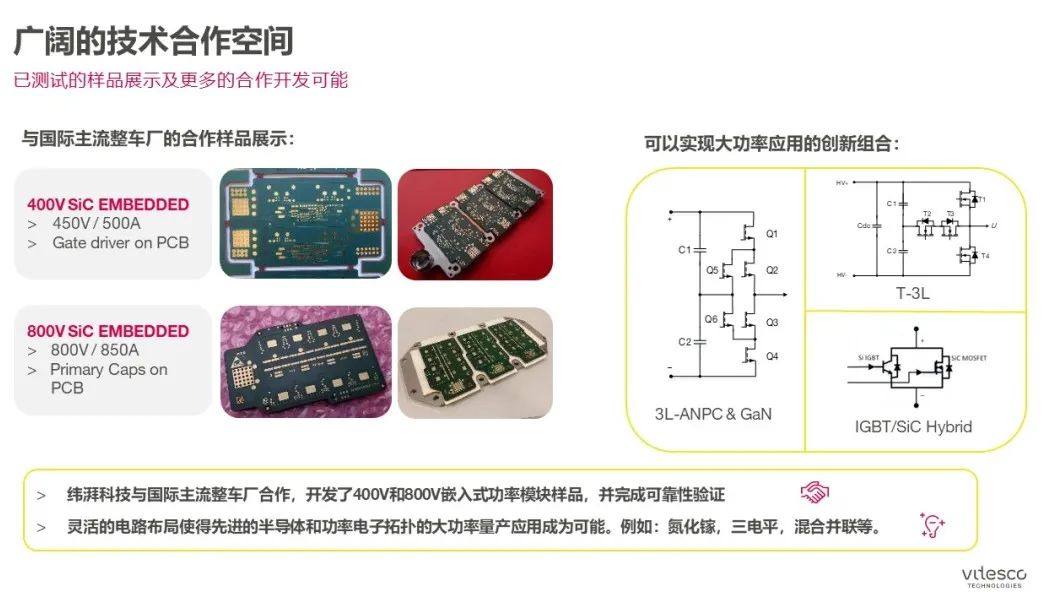
纬湃科技已经设计开发了基于400V和800V系统的功率模块样品,并完成首轮性能和关键可靠性验证。其中800V样品作为高性能产品的代表,每个功率开关使用8颗面积为20平方毫米的功率芯片,半桥模块PCB尺寸为70mm * 40mm,模块杂散电感降到1nH以下,压摆率超过每微秒25kV,单相输出电流峰值有效值达到850A。
PCB布局设计相对于传统封装设计更加灵活,大大加快了工程开发的迭代速度和客户交付速度。
同时,受到封装限制而难以在传统逆变器中实现的高级电路拓扑,如三电平、IGBT/SiC MOSFET混并等方案,都可以借助PCB嵌入式封装高度灵活性的优势而具有了产业化落地的可能。
根据我们的技术和商业评估,PCB嵌入式功率模块是一项非常有前景的封装技术,有望在在单位功率成本、功率密度、产品交付和迭代速度等方面远远超越传统封装,成为未来汽车功率电子行业新的方向!
原文始发于微信公众号(纬湃科技中国):李智文 | PCB嵌入式功率模块技术走势分析和应用前景
成员: 5306人, 热度: 153517
陶瓷 天线 通讯 终端 汽车配件 滤波器 电子陶瓷 LTCC MLCC HTCC DBC AMB DPC 厚膜基板 氧化铝粉体 氮化铝粉体 氮化硅粉体 碳化硅粉体 氧化铍粉体 粉体 生瓷带 陶瓷基板 氧化铝基板 切割机 线路板 铜材 氮化铝基板 氧化铍基板 碳化硅基板 氮化硅基板 玻璃粉 集成电路 镀膜设备 靶材 电子元件 封装 传感器 导电材料 电子浆料 划片机 稀土氧化物 耐火材料 电感 电容 电镀 电镀设备 电镀加工 代工 等离子设备 贴片 耗材 网版 自动化 烧结炉 流延机 磨抛设备 曝光显影 砂磨机 打孔机 激光设备 印刷机 包装机 叠层机 检测设备 设备配件 添加剂 薄膜 材料 粘合剂 高校研究所 清洗 二氧化钛 贸易 设备 代理 其他 LED