在传统的功率电路里,封装好的功率半导体是通过印刷电路板(PCB)或者汇流条(Busbar)和电路里的其他元件连起来的。但其存在寄生电感大(超10nH)、开关损耗高以及因热失配导致应力失效率高的问题,因此对于多芯片并联的SiC超级结器件,开发多层平面互连的高密度集成化封装技术,是提升其性能与可靠性的必要举措。
当前以PCB嵌入式为代表的新一代技术纷纷出现在各家的研发名单中。这一技术是通过将高压功率芯片直接嵌入PCB板(如SiC、GaN芯片),替代传统分立式功率模块,可实现电驱控制器的高密度集成与性能跃升。常规的功率半导体以分立模块形式焊接在PCB表面,通过铜排或引线连接,存在体积大、寄生电感高、散热路径长等问题。
PCB嵌入技术通过去模块化、去线束化、去散热器化,将功率半导体的集成度推向了新的高度。其热阻更低,开关损耗也极低。同样的出流要求,可使半导体的用量比框架式模块减少20% -30%。在WLTC循环损耗对比中,相较于800V SiC框架式封装,800V SiC嵌入式封装的能量损耗减少约60%,开关损耗和导通损耗降低。这使得逆变器尺寸减小、电机最高转速提升,同时降低电池电量需求,实现整车降本。而且在相同温度条件下,嵌入式功率模块的寿命是框架式封装的数倍。
尽管面临热应力、材料适配和量产成本挑战,其低电感、高密度、高可靠性的优势已在高性能电驱、工业电源等领域展现潜力。随着SiC/GaN普及和汽车电动化加速,该技术或将成为下一代功率电子的主流封装方案。
01.
此前,英飞凌和Schweizer Electronic合作,通过在PCB中嵌入一个48V的MOSFET器件,将性能提高了35%。这项技术成果的背后,是Schweizer提供的p²Pack解决方案。Schweizer在汽车48V应用方面已开展量产准备工作,同时也在着眼于下一代产品,研发用于400-1200V电压的嵌入式“宽带隙”半导体高压p²Pack。若进一步将功率开关与电容器一起嵌入,还能提高功率密度和可靠性,集成分流器还可将电流测量功能集成到PCB板内部。
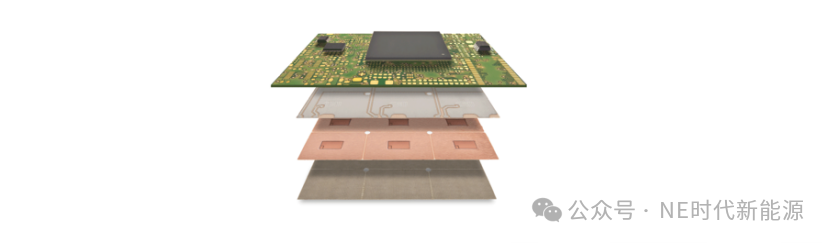
图片来源:Schweizer—48V p²Pack封装
英飞凌的方案就是把开关与电容器一起嵌入,其是将1200V CoolSiC™芯片直接嵌入PCB中,该芯片嵌入板由五个与主直流链路电容相连的连接器,就是五个大电容负责稳定整体供电。并配置了三个邻近MOSFET半桥的900VCeraLink™电容作为局部直流链路电容器,以有效抑制杂散电感。每个开关单元集成了一枚嵌入式S-Cell和一片20mm²的CoolSiC碳化硅芯片。
注:S-Cell是英飞凌经过100%电气测试的标准芯片。在p²Pack组件制造过程中采用S-Cell,能够大幅提升整体产量。同时CoolSiC芯片具备快速开关特性,而p²Pack所实现的低电感互连,能够为其提供最佳支持,充分发挥该特性优势。
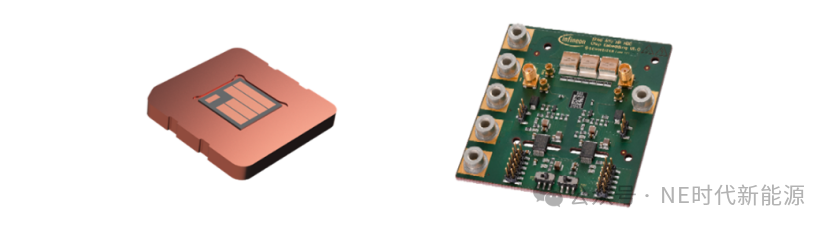
通过将栅极驱动器紧邻半桥布局并结合单板设计,实现低电感栅极回路、高速开关特性及信号振荡最小化。除了电流的传输路径短了,此方案还采用了引线框架设计,顶部触点使用铜填充微孔与厚铜层连接,代替了传统的键合线,极大地降低了寄生电感,可实现低电感互连。
从整个结构来看,p²Pack嵌入技术减少了无源器件、连接器等组件的使用。采用关键部件贴身布局、用特殊材料防过热、测量点直连避免干扰,既能扛住高压大电流,又能让工程师像用听诊器一样清晰监测每个细节。
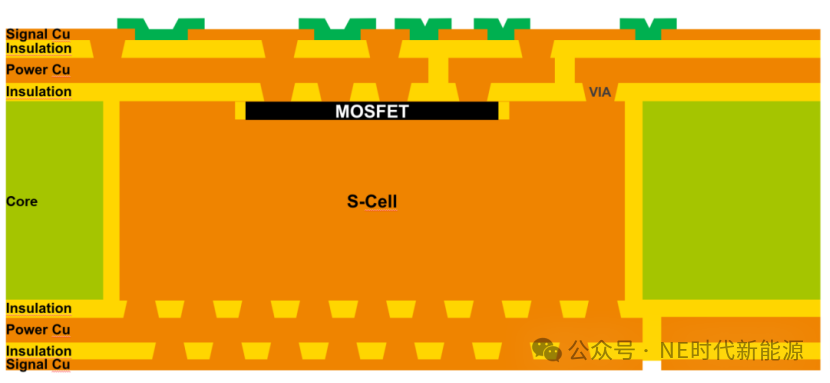
威睿前段时间也推出了一款内埋式封装电驱控制器(Chip Embedded Power Unit,CEPU),其是采用功率模块芯片和印刷电路板直接埋嵌封装以及珊瑚翅片高效冷却水道设计,同时还采用了深度集成的薄膜电容技术,提升了产品的功率密度。相对于上一代产品,其功率密度提升了约55%,体积减小了约51%,Z向高度小于2个壹圆硬币的外径尺寸。使得该产品更加易于系统集成。
其采用的叠层主功率回路与多层走线设计,杂感降低约65%,激光镭射工艺取代传统绑定和焊接,提升工作寿命与整车可靠性。超低杂散使开关损耗降低约50%,提升电驱系统工况效率与续航,还通过提高载波频率优化整车NVH表现。该产品基于模块化、平台化理念,能适配不同功率段与250V- 1000V母线电压。目前已完成样品台架测试,进入产业化准备阶段,相关项目入选浙江科技计划。
采埃孚的嵌入式逆变器(Chip Inlay Power Board, CIPB),其可自定义PCB形状接口,减少寄生电感和电阻,提高电气性能,能轻松适配多样整机外形和固定点需求,满足主机厂不同车型电驱动结构的复杂应用场景。其长宽尺寸约为两个iPhone16并排大小,却能输出≥600Arms电流。
采埃孚CIPB功率核心是通过合理设计功率回路,优化从电容到功率交直流路径等,提升并联功率半导体芯片均流性和回路杂散参数,减小功率半导体芯片开关和导通损耗,从而提升系统效率,在动静态性能上优于传统功率模块。
传统功率模块限制逆变器机电一体化布局,而采埃孚CIPB基于芯片内嵌技术的灵活性,提供了不同的逆变器系统设计思路,使布局更紧凑灵活。相较于采埃孚一代同类型产品,1200V SiC逆变器系统功率密度呈类指数增长,通过优化芯片布局等手段,逆变器层级功率密度超过120kW/L。
2023年起,采埃孚的CIPB技术在1200V SiC逆变器平台产品中完成功能、性能验证及关键可靠性验证。基于AQG324的耐久性测试显示,CIPB方案在芯片内嵌功率单元新型失效模式的测试中表现优异,在分钟级功率循环、热冲击、高温高湿环境下,CIPB热阻变化远低于传统功率模块,耐久寿命显著优于传统封装模块。
麦格纳新一代的800V电驱动系统也是一个嵌入式解决方案,采用了MPT 800V SiC芯片,最高峰值电流530Arms,每个半桥使用了250mm²的SiC材料,模块采用单侧冷却设计。
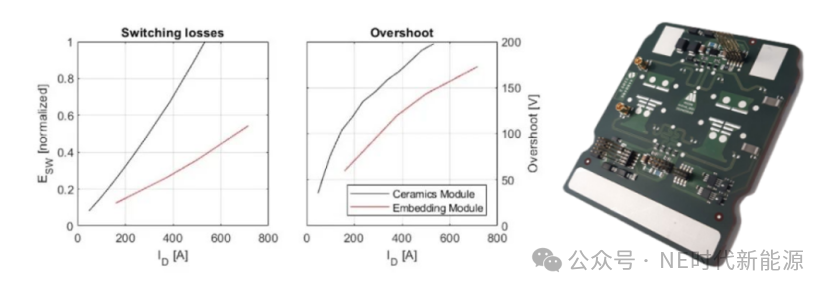
02.
如何把芯片“埋进”电路板,主流的方法有三种:一种是把芯片粘在底层铜板→铺玻璃纤维预浸料(预留芯片坑)→盖铜箔→高温高压压成一体→激光打孔镀铜连线。这种适合大尺寸芯片,是德国弗劳恩霍夫研究所1999年首创,但芯片表面需镀铜(但传统芯片是铝皮,得先“穿铜盔甲”)。
另一种是在厚铜板上精准挖出芯片坑→放入芯片(与铜板表面齐平)→铺玻璃纤维胶布(无需预挖坑)→跟上述的方法一样压合后打孔连线。这个方法就是Schweizer的p²PACK技术。
还有一种是把芯片用胶水粘在薄铜箔→多层预浸料覆盖(部分挖坑,部分不挖)→上下激光打孔→镀铜连通两面。无引线键合,寄生电感极低,适用于GaN氮化镓模块。主要是奥地利AT&S的ECP技术为代表。
这些嵌入技术有两种不同的集成概念。第一种是把嵌入技术用于制作器件级的PCB功率组件,这些组件像表贴器件(SMD)一样,连接到主电路板上,给传统基于引线框架的分立封装提供了新选择。
第二种概念是把PCB嵌入同时用于器件级封装和板级封装。这就得在芯片嵌入后,再进行额外的层压,增加布线层,并且在连接散热器的封装底部做好电绝缘。为了高效散热,得用导热又电绝缘的预浸料材料。把多个嵌入式功率半导体放在一块PCB上,并且做好内部电气隔离,这就成了PCB功率模块。再把栅极驱动器、去耦电容器、温度或电流传感器这些组件,通过SMD连接到PCB功率模块上,就做出了嵌入式“智能功率模块“(IPM)。极端情况下,把整个电源电路都集成在嵌入式PCB上,就形成了完整的板上系统。
这里其实还有不少问题比如覆铜技术,在晶圆级电镀过程中,当铜层厚度达到30~50µm时,芯片可能会产生超过100µm的弯曲。这种弯曲可能会对芯片的后续封装和性能测试产生不利影响。通过在芯片的正面和背面同时镀铜,可以平衡内部应力,从而减少弯曲。还有一些热应力以及微孔形成方面的问题。
原文始发于微信公众号(NE时代半导体):嵌入式是未来功率模块的终极路线吗?