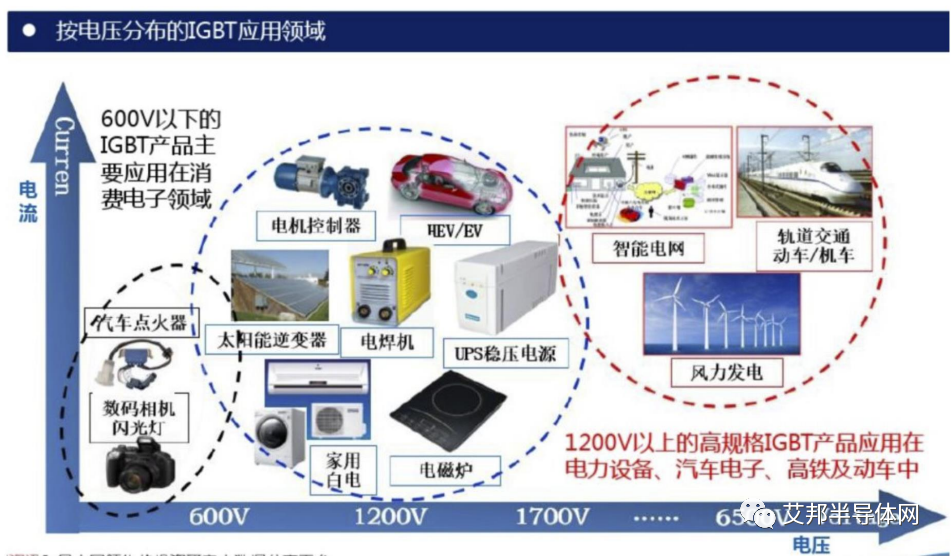
阅读本文前,欢迎识别二维码加入艾邦IGBT产业链微信群及通讯录。
IGBT应用方式和封装要求
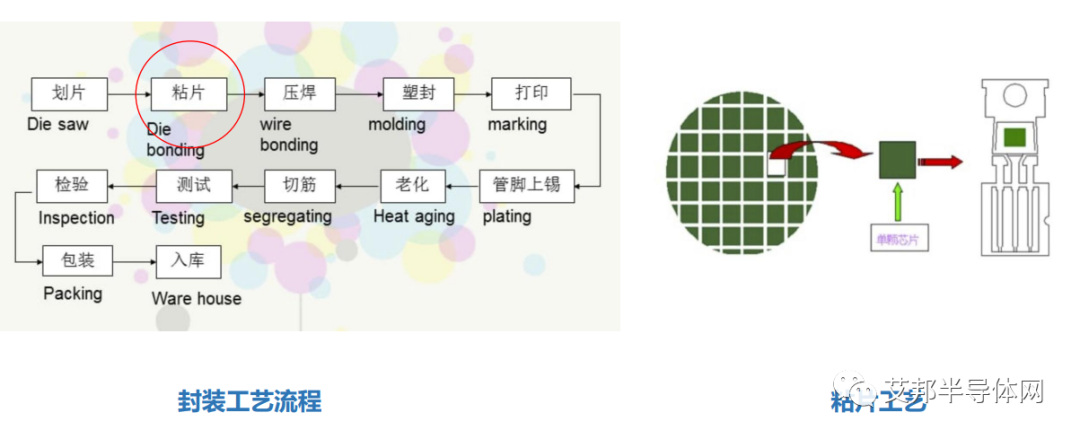
IGBT单管封装粘片工艺及其问题
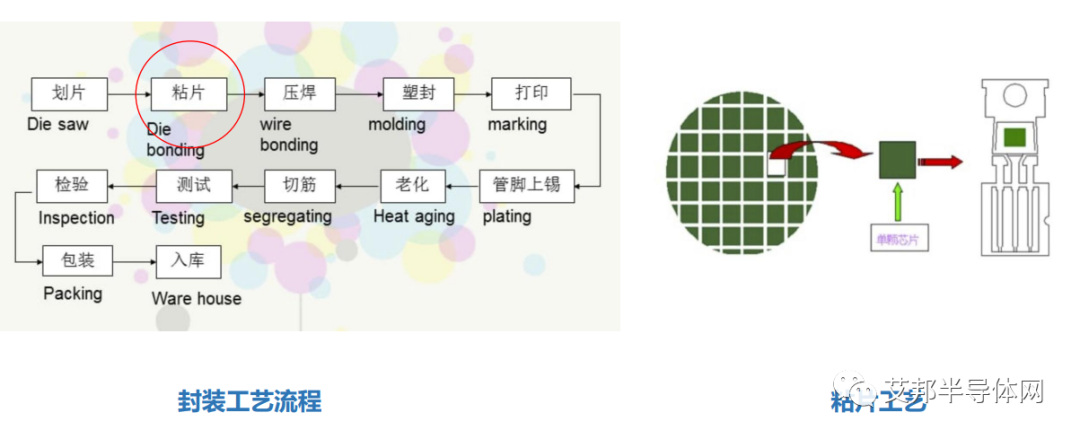
-
在粘片过程中,框架需要经过两次加热,若采用同样熔点的焊锡,则粘第二颗芯片时,会导致第一颗芯片焊锡的融化,从而导致位置偏移、焊锡厚度不均匀、增加气泡等问题。若采用更低熔点的焊锡粘接第二颗芯片,则会增加串联电阻,影响使用;
-
框架经过两次升降温,会造成物理机械性能上的影响,升温降温过程中的热胀冷缩可能会造成框架的变形,若变形量过大,影响第二次粘片后的过片,造成卡料而报废;框架头(IGBT芯片和快恢复二极管芯片所在位置)经过热胀冷缩后产生变形,造成注塑后露铜问题,在应用时可能会导致短路。
-
两台粘片设备会导致设备成本、能耗增加、占用厂房面积和操作人员的增加。
IGBT单管封装双芯片粘片工艺
-
两颗芯片同时粘,可以采用同样熔点的焊锡,粘第二颗芯片时不会引起第一颗芯片位置偏移,焊锡厚度均匀,空洞率低; -
框架只经过一次升降温过程,不易因框架变形而影响第二颗粘片时的过片,造成卡料报废,不易使框架头变形,造成露铜问题; -
降低设备成本和能耗,提高生产效率; -
减少厂房占地面积和操作人员。
-
采用计算机控制的伺服电机系统,运用摆臂+三轴联动配合的方式,同时实现两种不同芯片的高精度键合功能;
-
优越的结构设计:两套独立芯片工作台机构,一次加热完成两颗不同类型芯片的粘片工艺;
-
优越的过程控制:图像识别和自动寻位、θ角度修正技术,提高了粘片的灵活性、稳定性;
-
可调气体保护:升级版多温区可调节气体保护装置;
-
可调焊接压力:音圈电机实现压力无级电动调节;
-
自动送料、过料、收料;
-
采用计算机控制,全中文操作界面,更精确、方便的操作;
-
支持Mapping文件;
-
合理的占地面积3.1M ²。
-
生产速度UPH视具体产品来看,TO247为2000/小时,TO220为3000/小时;
-
固晶后实测粘片位置精度可以控制在±70μm,偏转角度控制在±2°以内;
-
焊锡层厚度在20μm-75μm范围内可调节,极差≤40μm;
-
整体空洞率<5%,单个<2%。
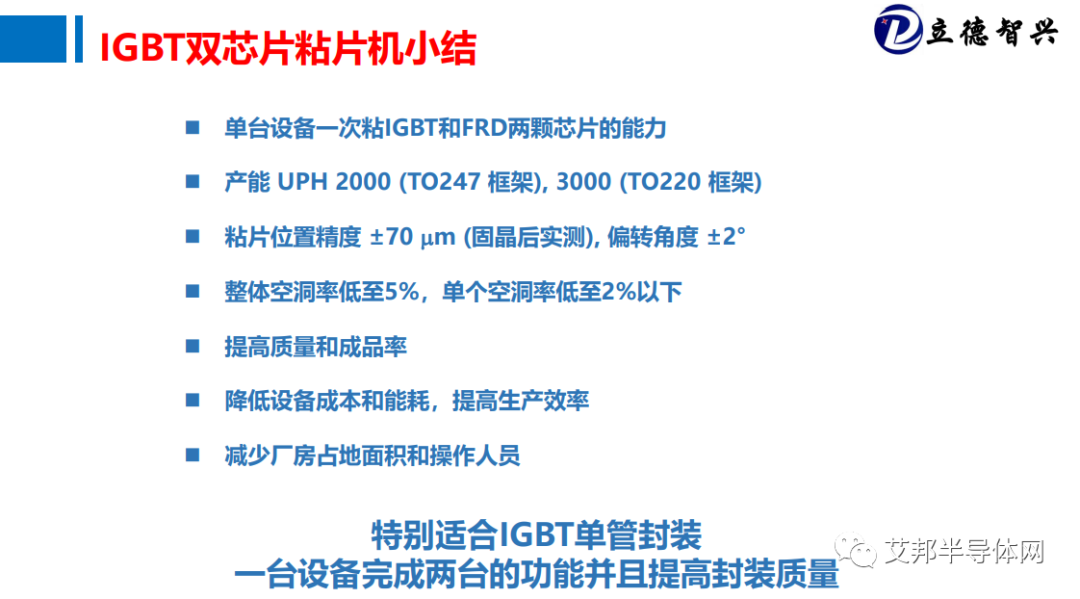
为加快产业上下游企业交流,艾邦建有IGBT产业链交流,目前已有英飞凌、华润微电子、比亚迪、中车、芯能半导体、晶越半导体、西安卫光、博敏电子、华清电子等IGBT产业链上下游企业加入,欢迎识别二维码加入产业链微信群及通讯录。
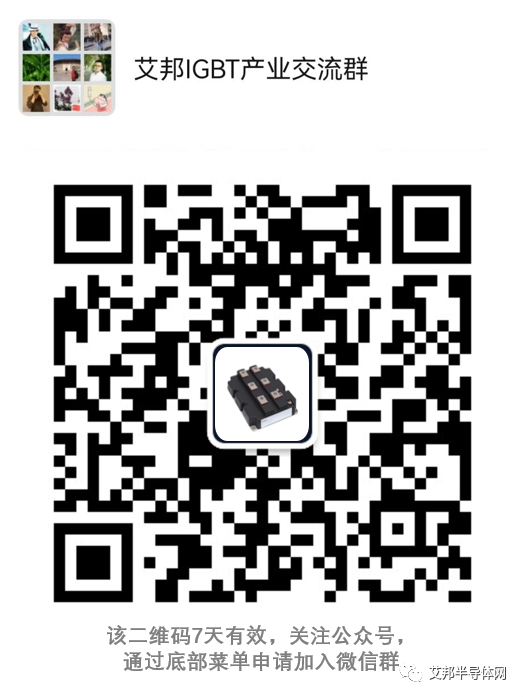
推荐活动:【观众预登记】第五届精密陶瓷暨IGBT产业链展览会(深圳宝安 8月29-31日)
8月29-31日
深圳国际会展中心8号馆
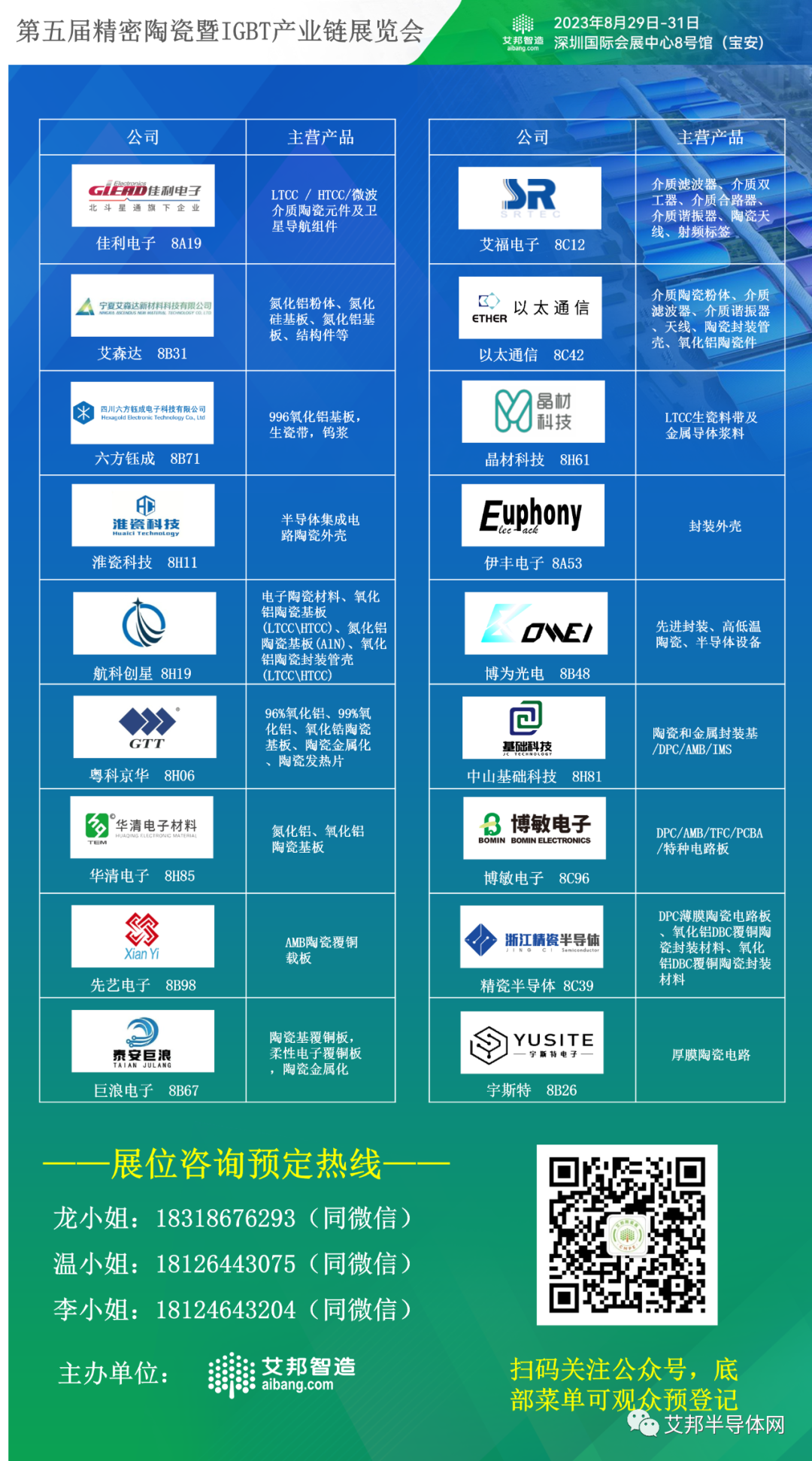
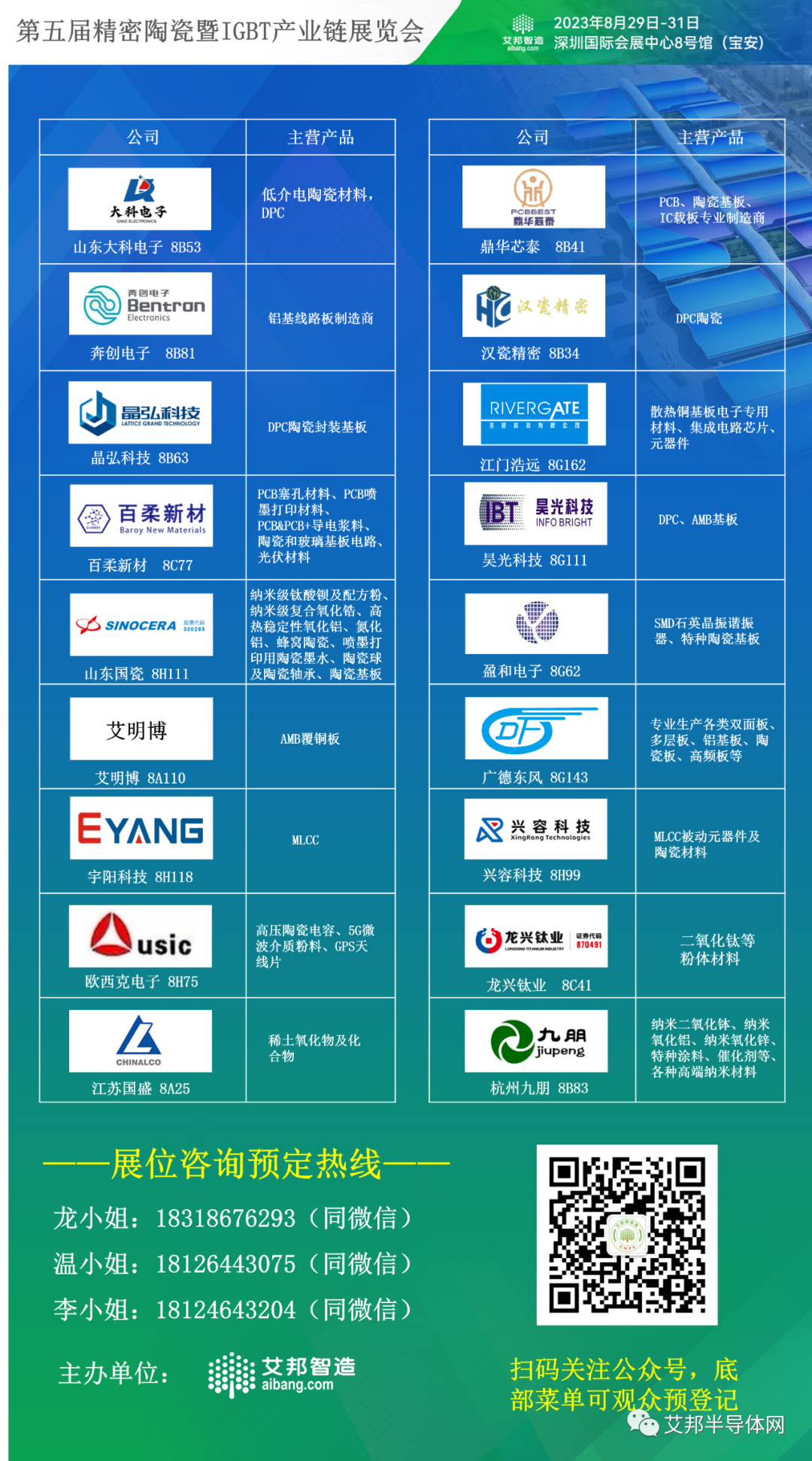
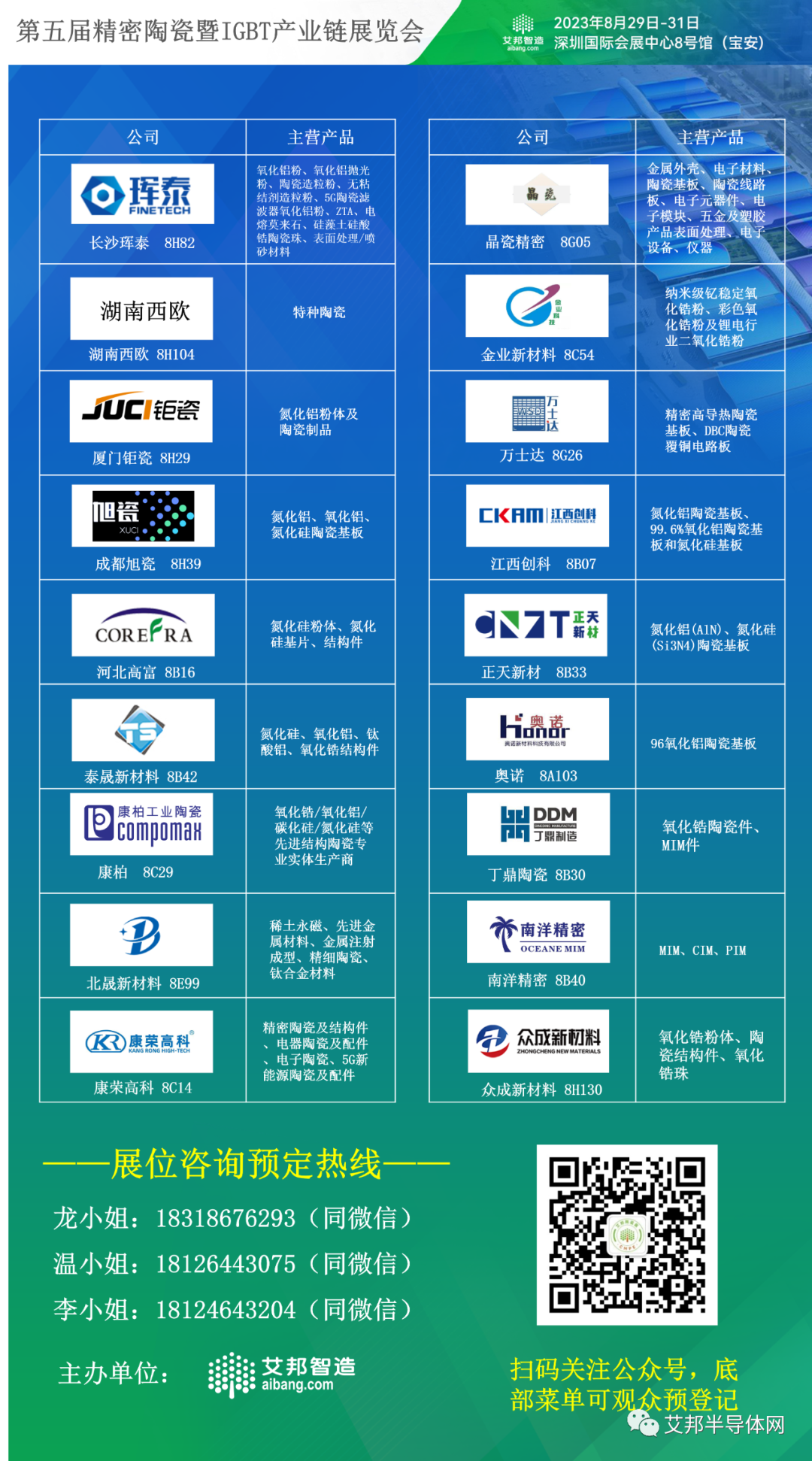
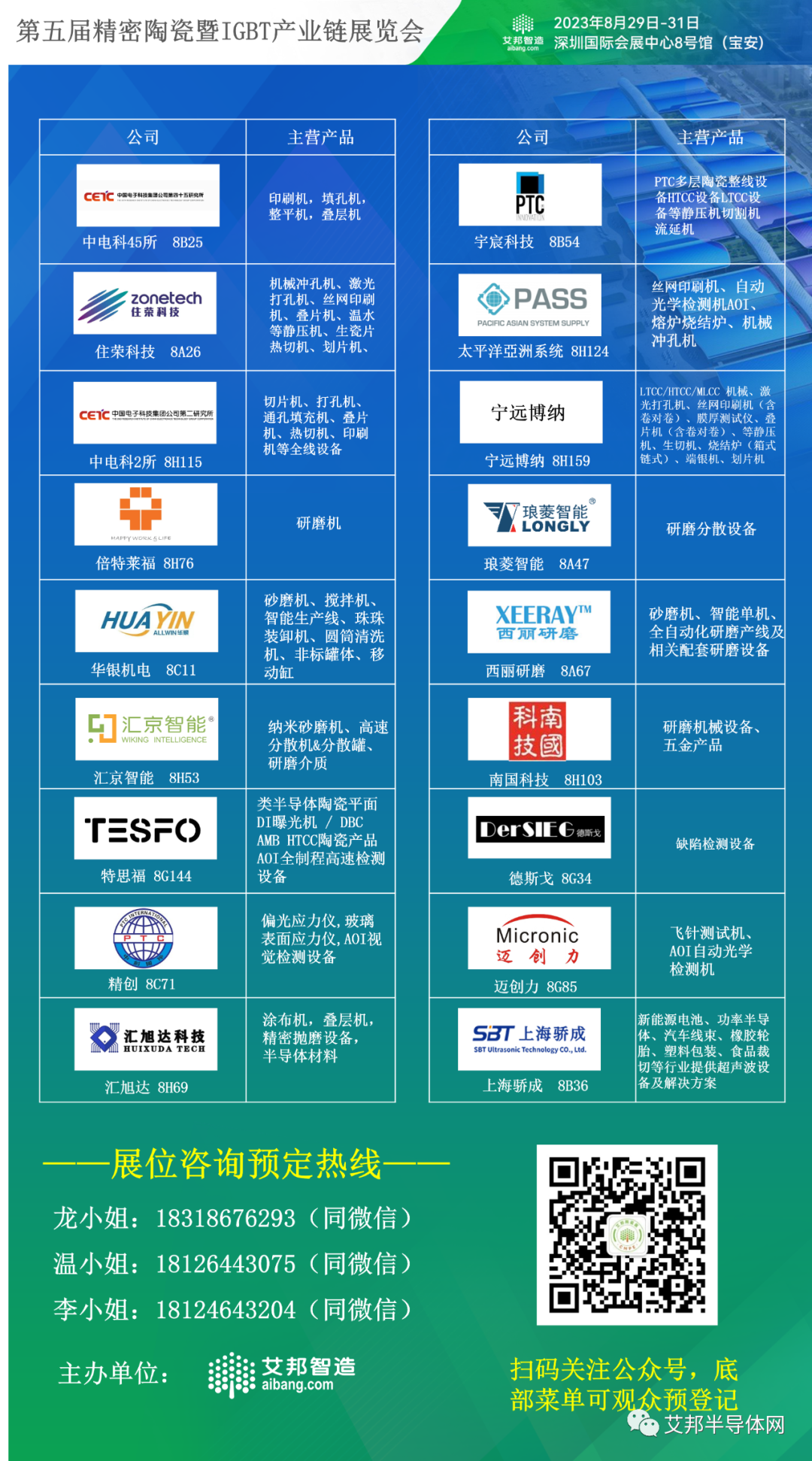
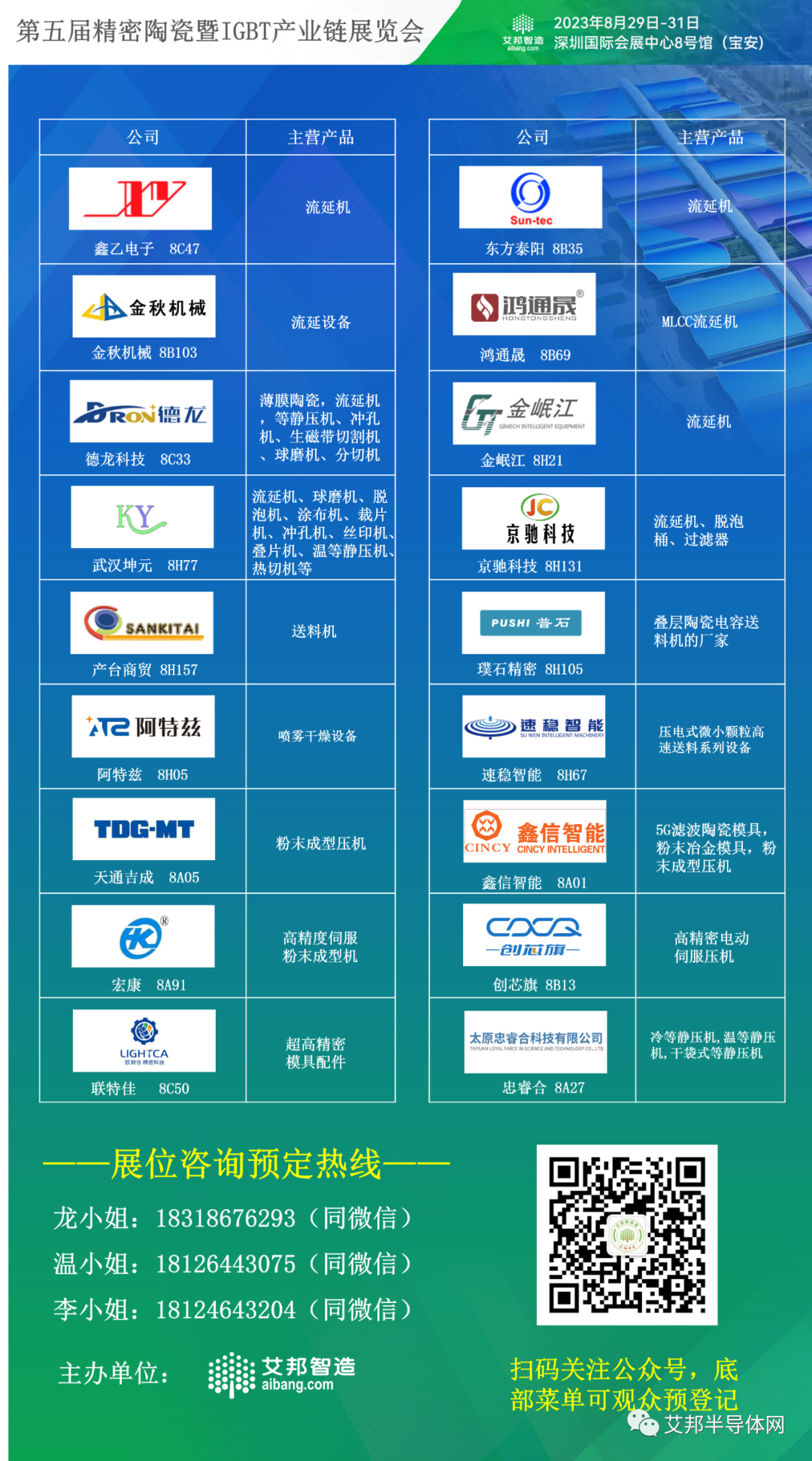
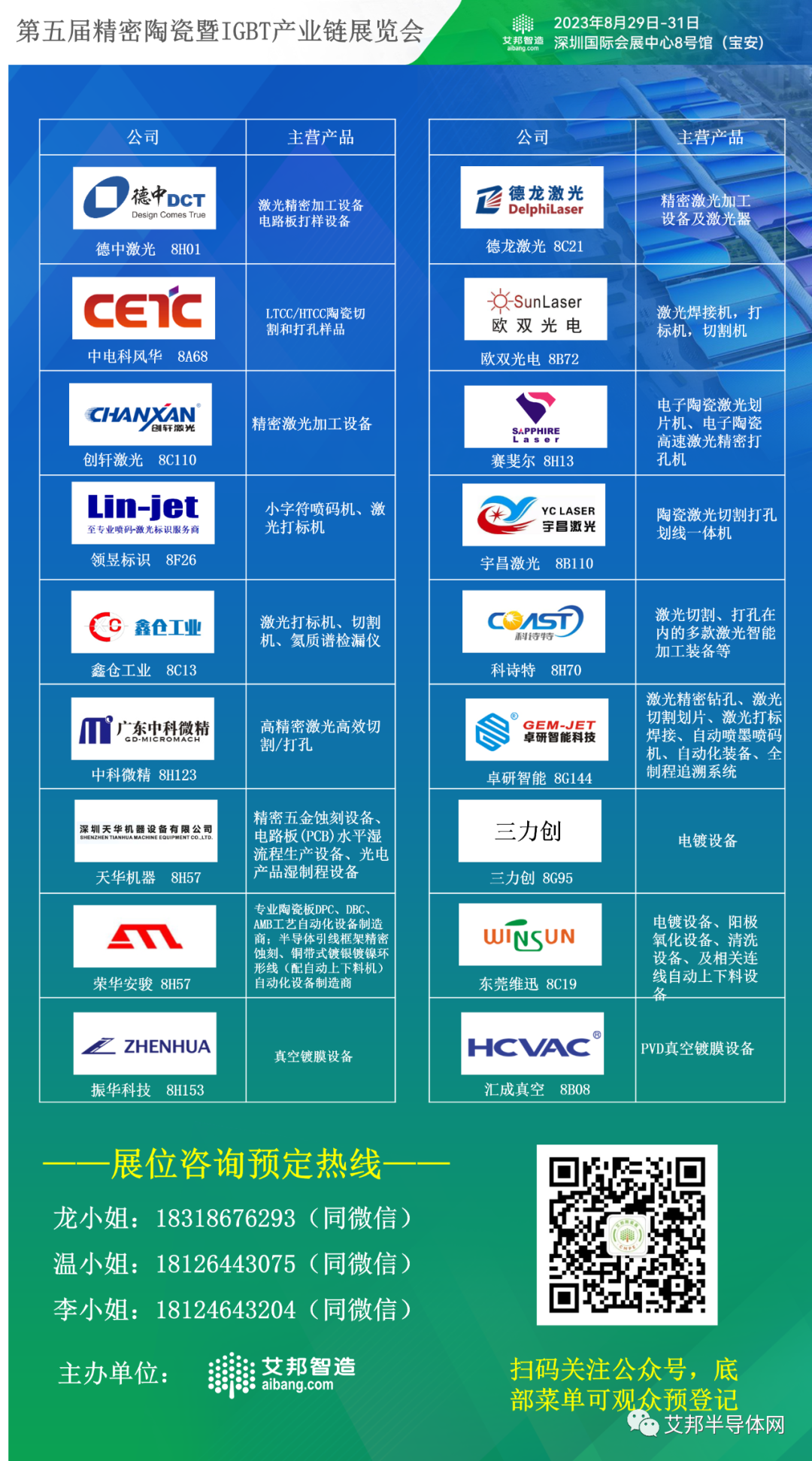
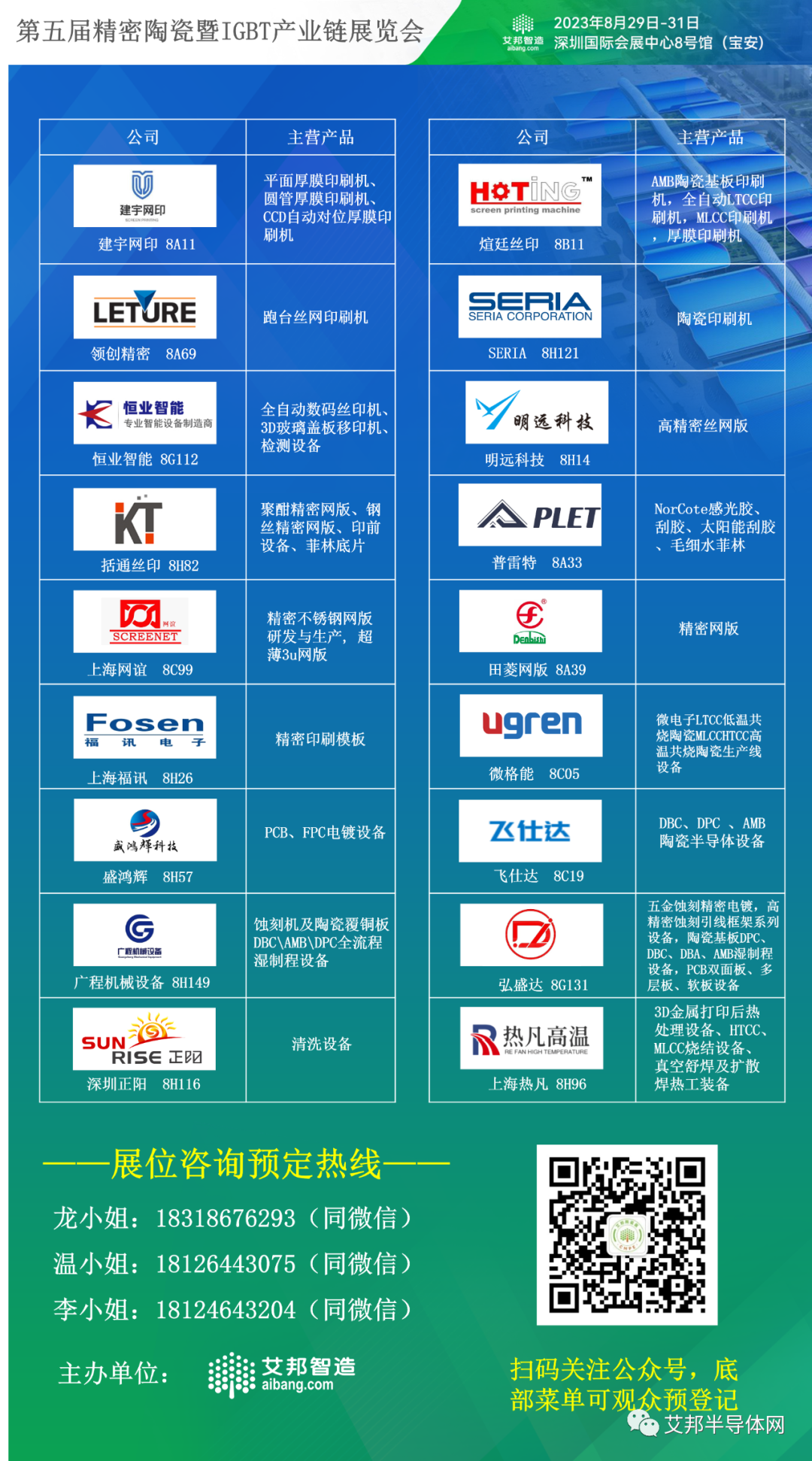
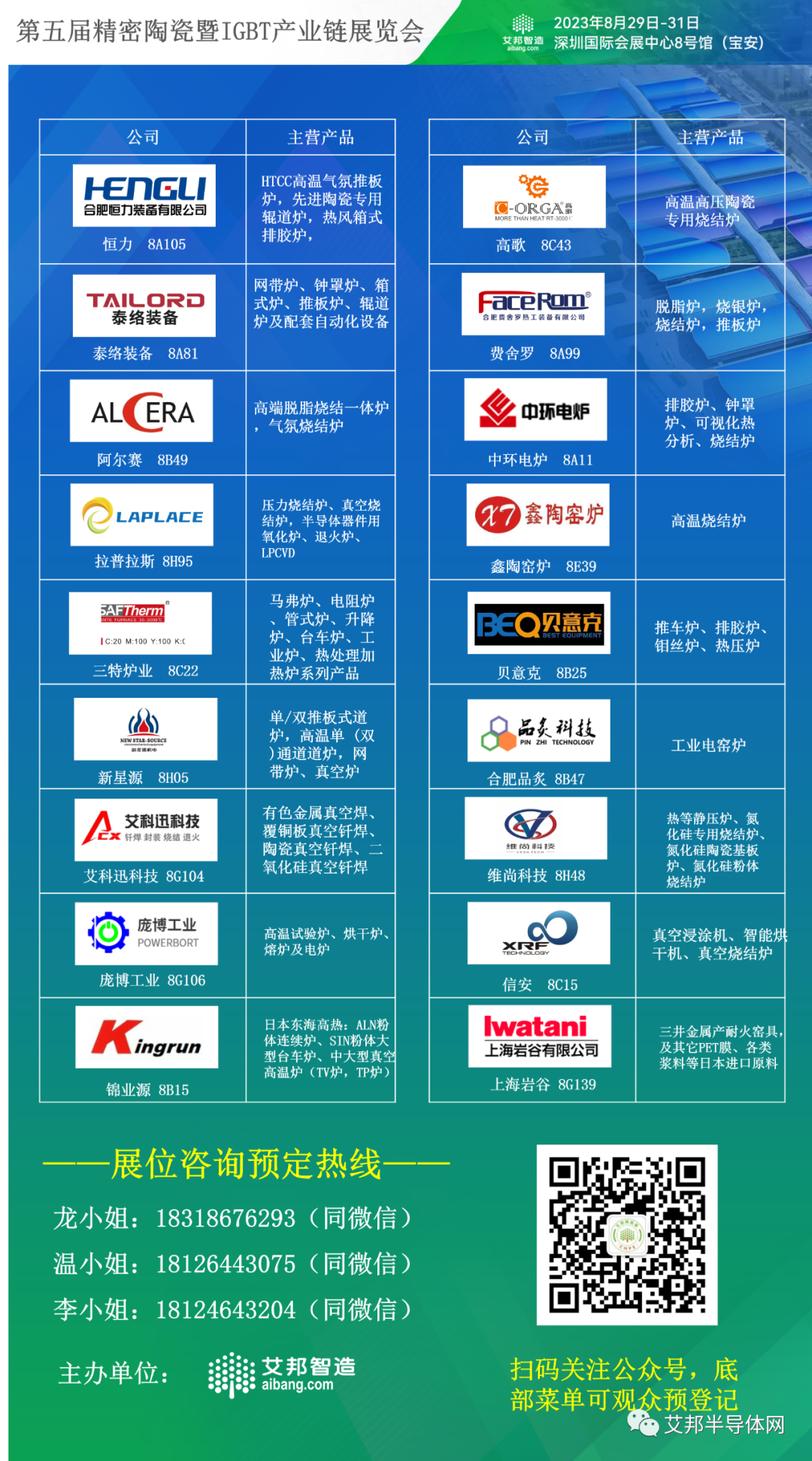
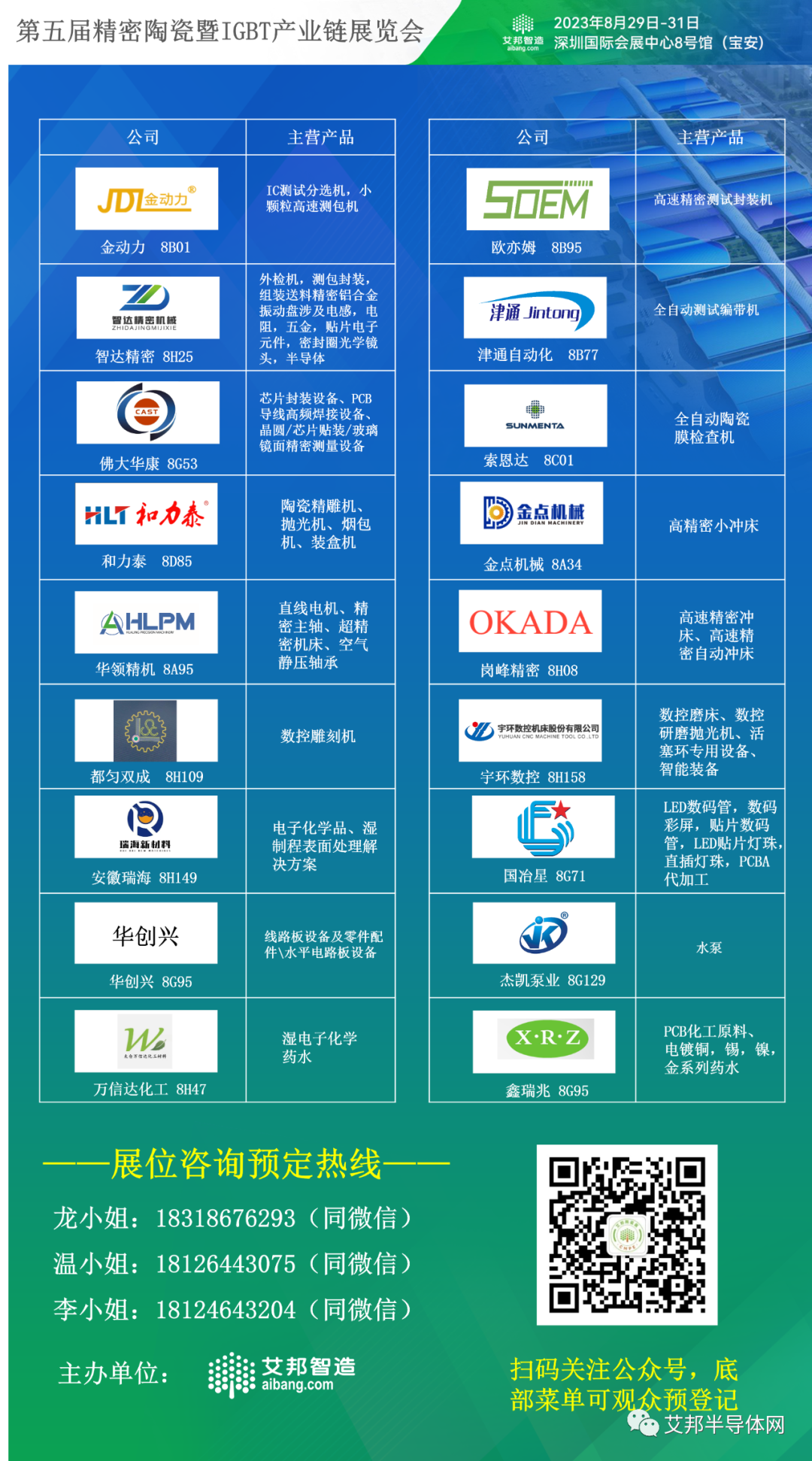
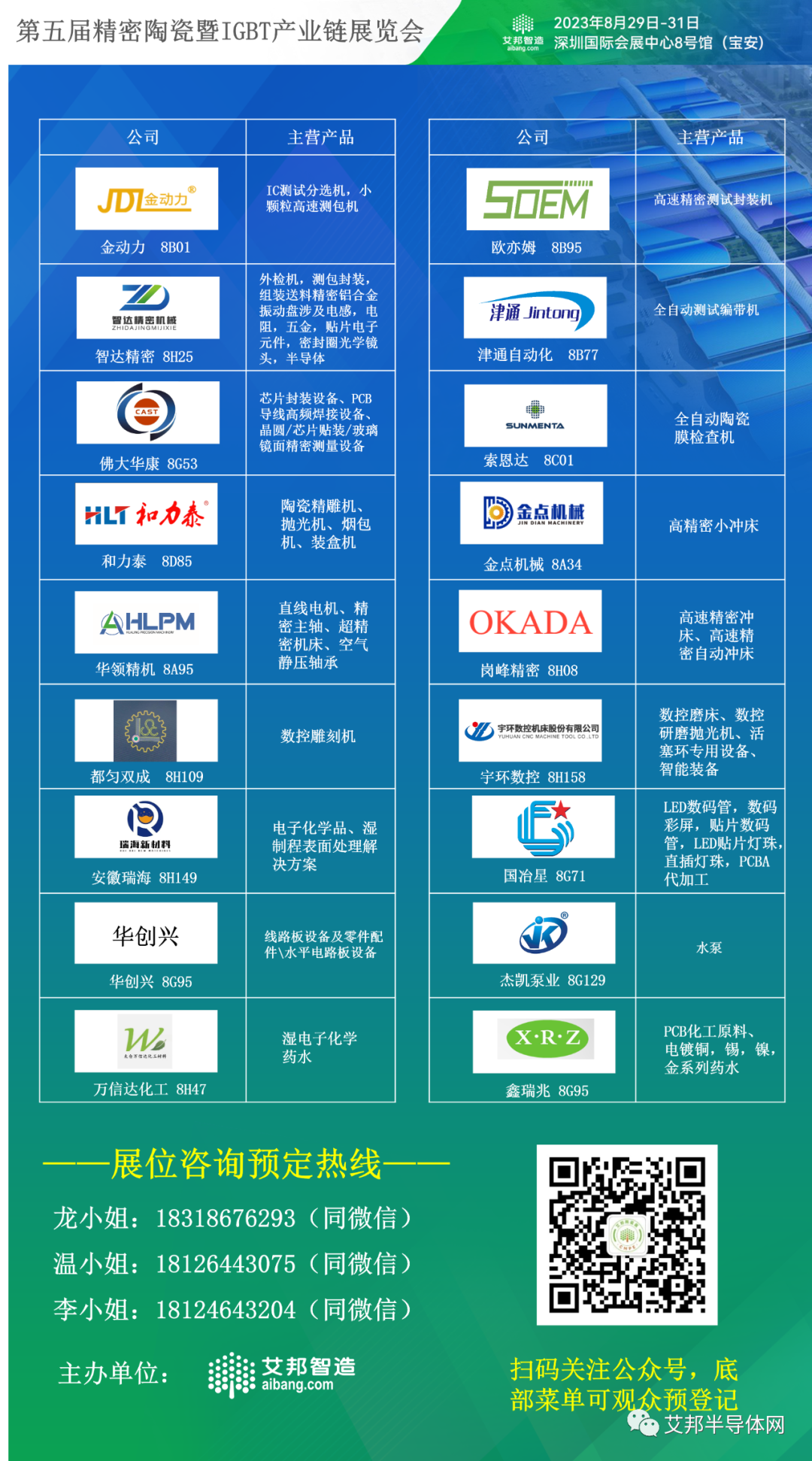
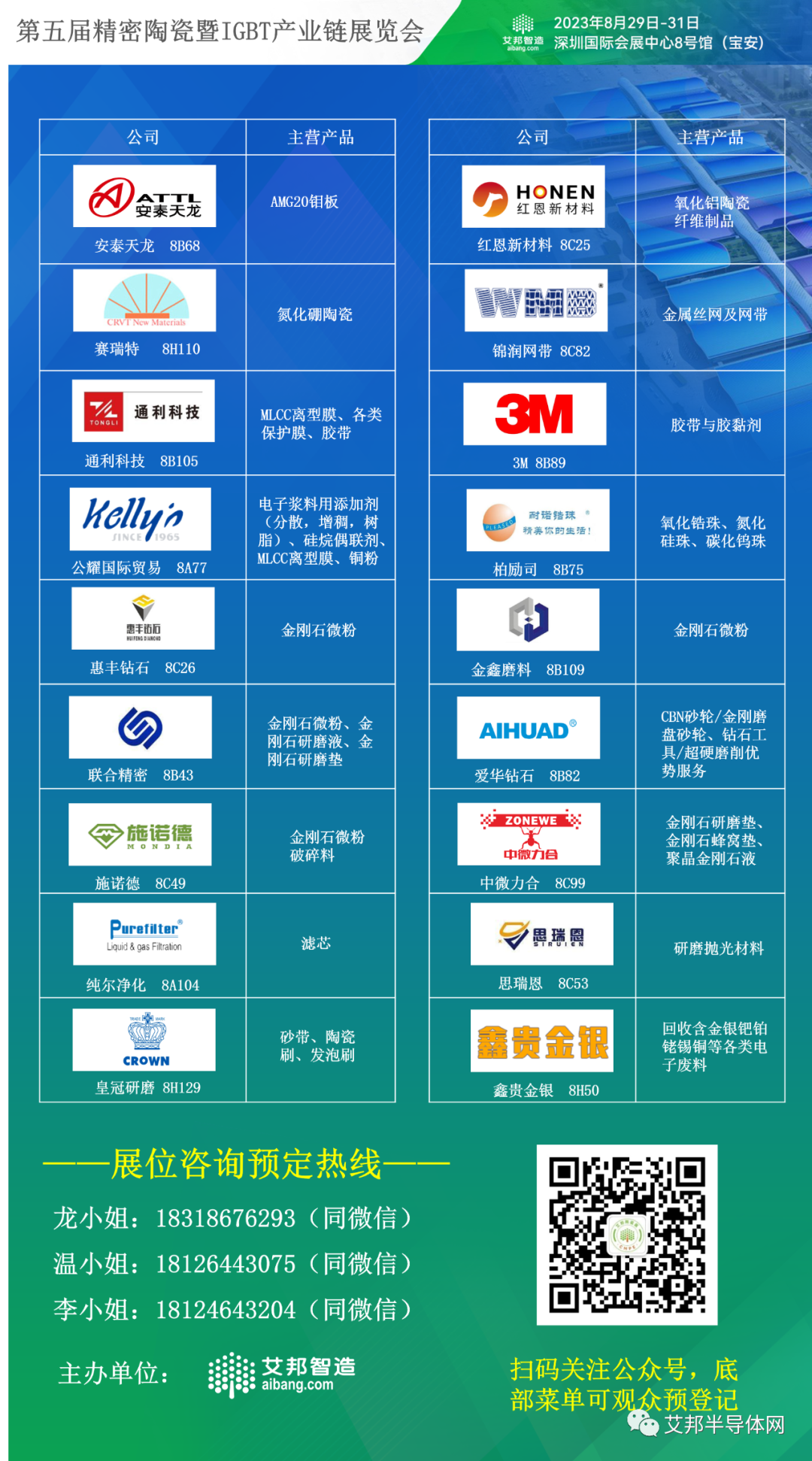
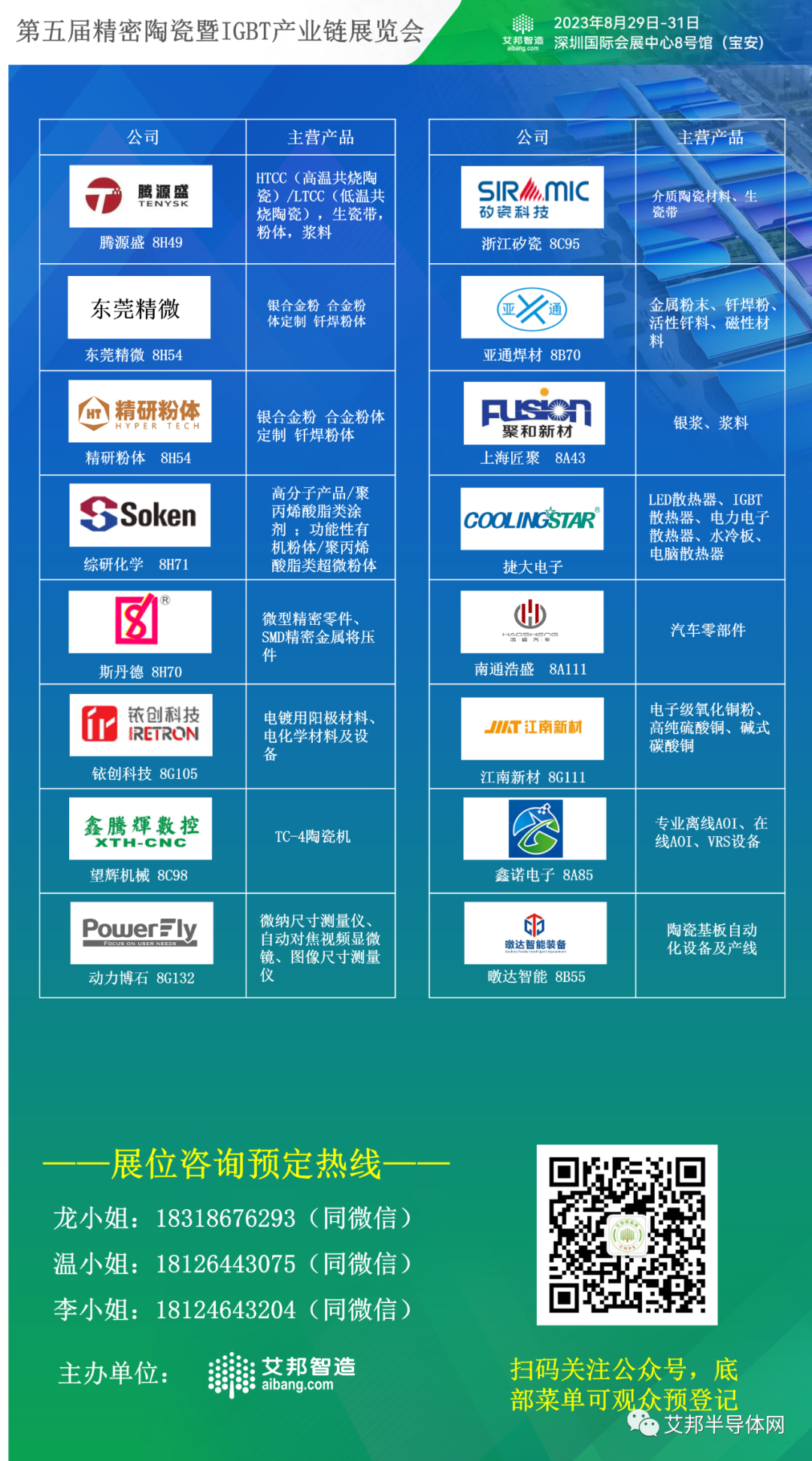
原文始发于微信公众号(艾邦半导体网):双芯片粘片工艺实现IGBT单管优质高效封装
一颗芯片的制造工艺非常复杂,需经过几千道工序,加工的每个阶段都面临难点。欢迎加入艾邦半导体产业微信群:
长按识别二维码关注公众号,点击下方菜单栏左侧“微信群”,申请加入群聊
为加快产业上下游企业交流,艾邦建有IGBT产业链交流,欢迎识别二维码加入产业链微信群及通讯录。
长按识别二维码关注公众号,点击下方菜单栏左侧“微信群”,申请加入群聊