摘要
功率模块封装受到近期 SiC 芯片发展的挑战。如今,额定电流高达 100A 的 SiC MOSFET 芯片已上市。汽车应用需要高于 800A 额定电流的大电流快速开关 SiC MOSFET 功率模块。为了达到这些功率水平,需要大量并联 SiC 芯片。
这种大电流功率模块的设计面临三个主要挑战:
首先,由于 SiC 器件的高开关速度,换流回路电感必须显着提高到 4nH 以下的水平。
其次,由于 SiC 芯片尺寸的限制,许多芯片必须并行工作,这需要电源模块内部的电源和栅极电路非常对称的布局。
第三,必须优化直流母线电容器连接,以保证总换流电感低于 6nH,以避免不受控制的过压。
为了保证功率模块和直流母线电容器设计之间的可靠连接,焊接连接是首选。如今,许多大功率模块仍然采用螺纹连接,这会增加制造成本并面临长时间的连接电阻变化。
本文介绍了一种采用 3D 设计的新电源模块:
1)DC+ 铜排一层;
2)DC- 铜排一层;
3)两层重叠并保证非常低的换流电感,如图 1:
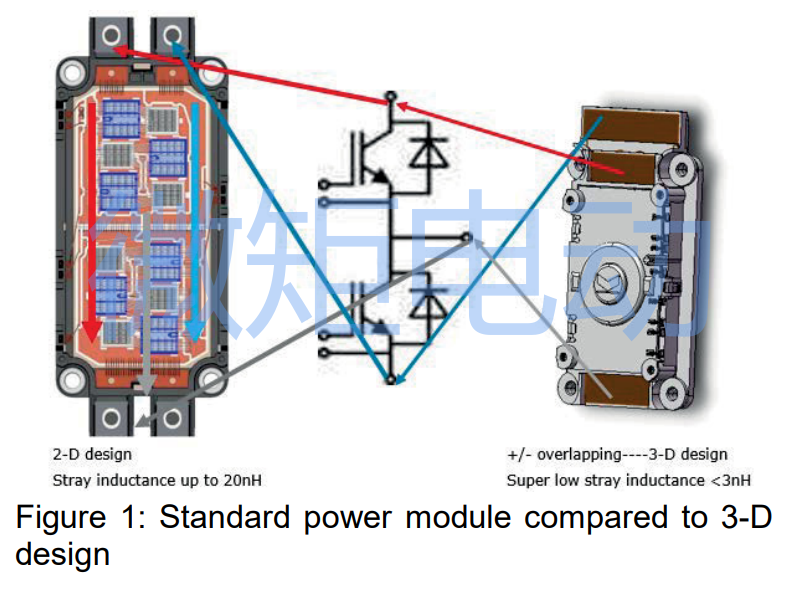
要实现具有焊接端子的低杂散电感模块,必须解决两个新的主要挑战:
1)如何设计保证低电感的焊接端子?
2)如何设计焊接设计中的直流母线电容器连接?
在本文中,我们将介绍:
1)采用优化的 SiC 芯片设计的新型功率模块 eMPack 并解释 3-D 设计技术,如图 2;
2)引入新的互连技术,不使用键合线的 SiC 芯片,如图 3 ;
3)可焊接连接技术,如图 4;
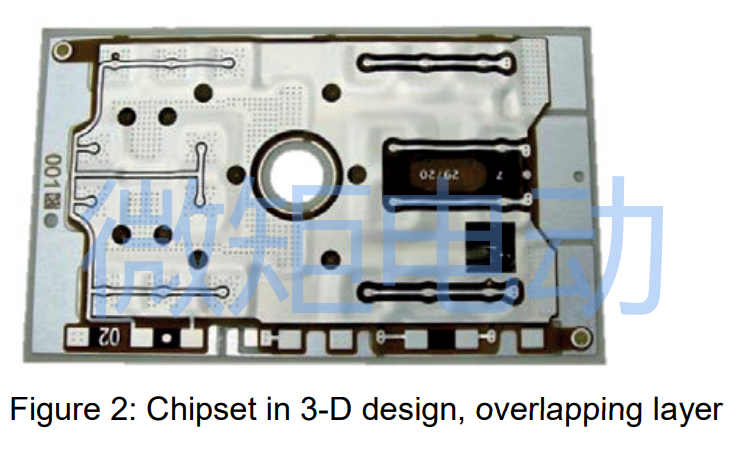
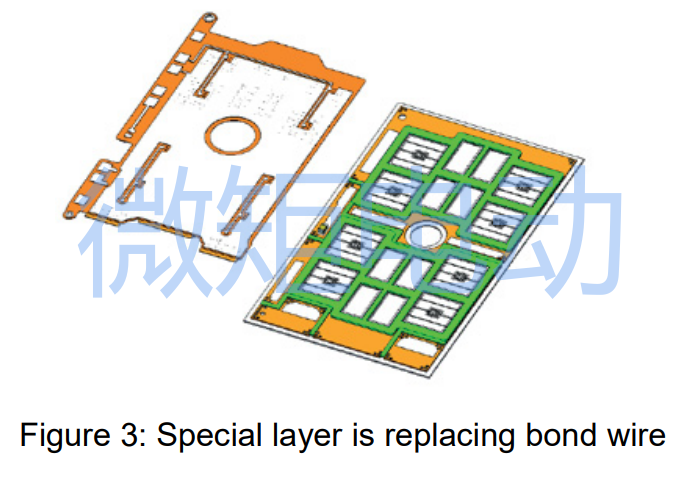
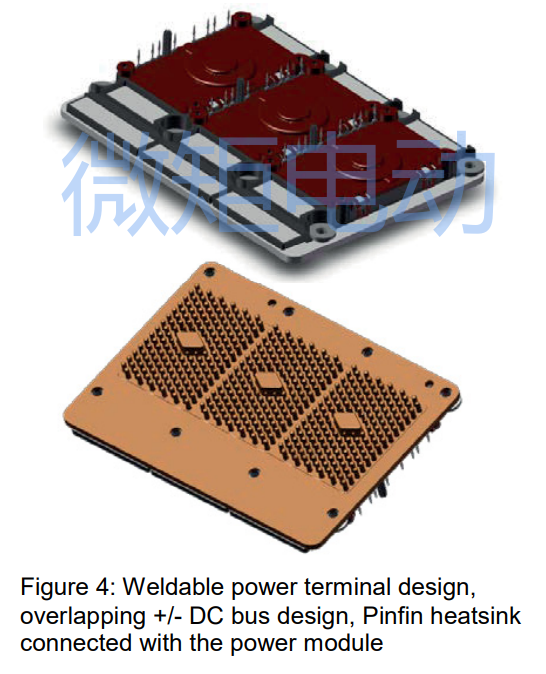
1. 功率端子设计
商用功率模块(图 1)总是使用类似的功率端子结构。DC 和 DC- 是并联的,一些方法试图通过外壳内部的特殊设计来降低电感,根本问题解决不了。功率端子之间的距离会产生杂散电感,并且与直流母线电容器的连接采用类似的设计,并带有额外的杂散电感。
图 5 至图 7 展示了Semikron对杂散电感的优化设计:
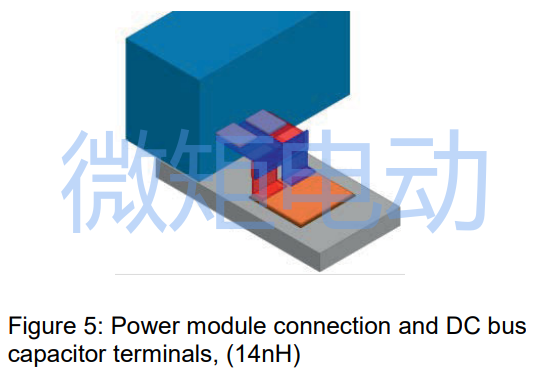

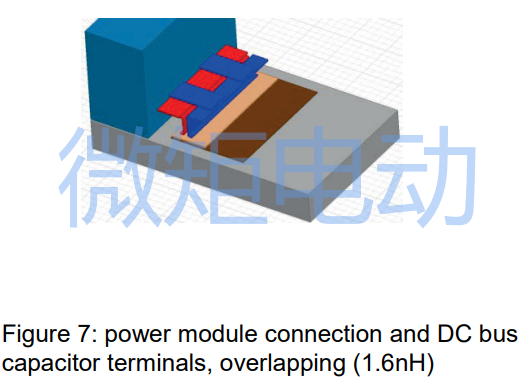
叠层的功率端子设计将保证低杂散电感并保证快速开关过程中的低关断电压。
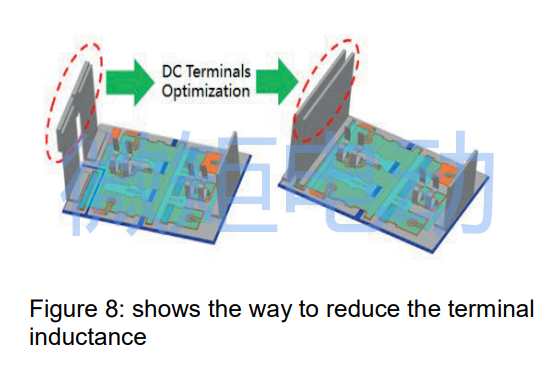
2. 焊接连接
在大批量生产过程中,螺纹端子会耗费时间(金钱)并且会产生可靠性问题。可焊接端子易于在每个生产过程中实施。许多激光焊接设备供应商可以提供优质的服务并帮助建立生产线。在焊接过程中,连接部件之间必须实现“0 间隙”。必须向可焊接部件提供一定压力。与螺纹端子相比,焊接连接将提供非常低的接触电阻, 5mm^2的焊接面积电阻<4uΩ,损耗 < 1W@500A 。
激光焊接功率还应需要仔细设计,焊接过程中工艺顺序也需要进行定义。
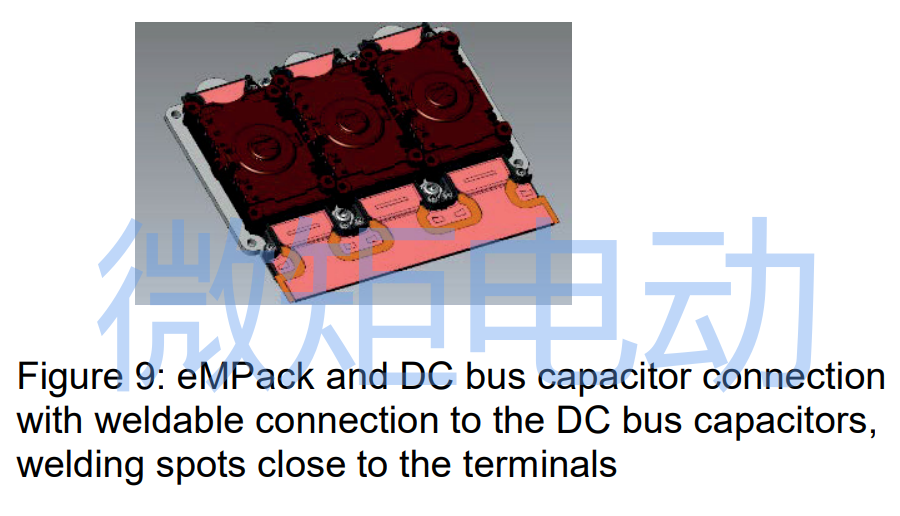
3. SiC芯片的DCB设计
SiC芯片非常小(大约25mm2),并且在13mOhm范围内有一个Rdson。为了达到更高的功率,并联是必须的。eMPack特殊的柔性电路板设计(而不是绑定线)保证了均匀的温度分布,以实现大电流(900A rms)的最小化DCB尺寸。
叠层结构(图10)节省了DCB设计的空间。DC+/-是一个3D设计,而不是传统的2D设计。通过这种特殊的设计,可以实现低换向电感通过这种特殊的设计可以实现低换向电感。此外可以实现更高的电流密度。
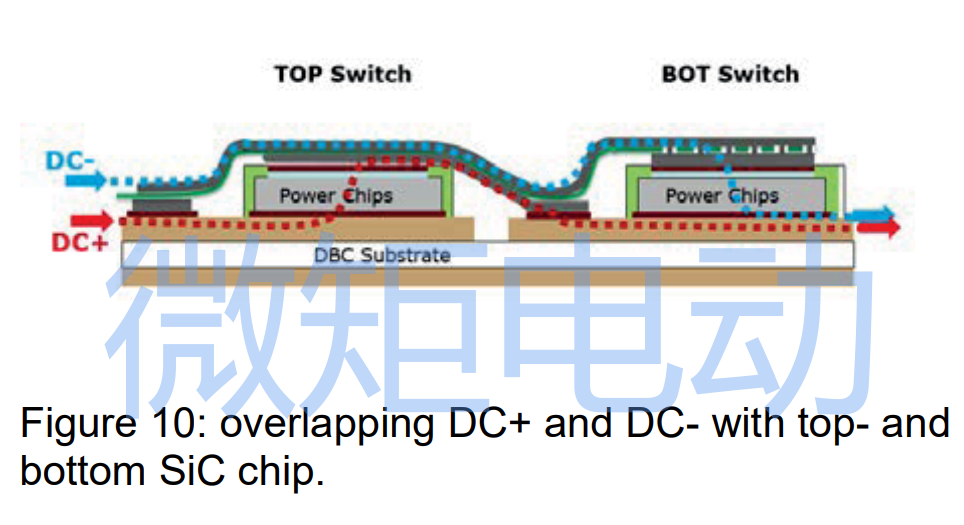
叠层式设计可以实现换向电感在1nH范围内。WBG(SiC)器件可以充分发挥性能。DCB通过材料优化以达到优化的热阻。
4.直流母线电容连接
eMPack需要低电感连接的电容器设计,传统的电容器设计有几个端子的传统电容器设计不适合用于本功率模块的连接。
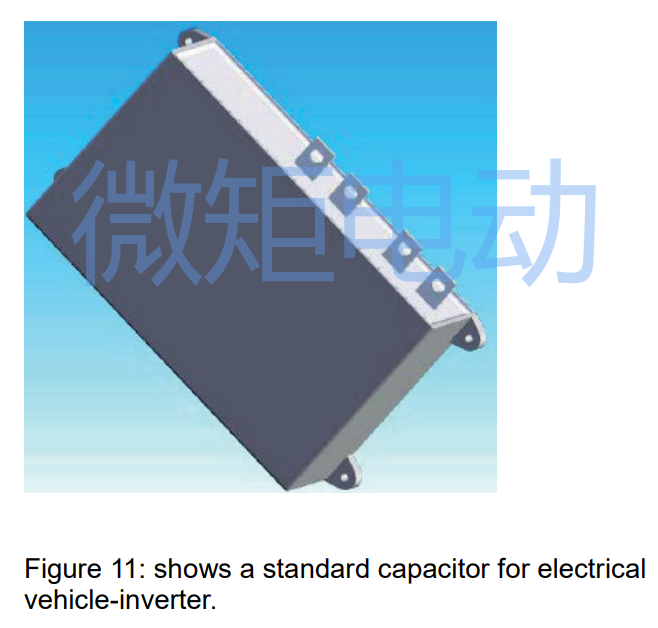
传统直流母线电容器并没有为低杂散电感连接到功率模块而进行优化。改善杂散电感可以通过为功率模块提供更多连接端子的电容器来实现。
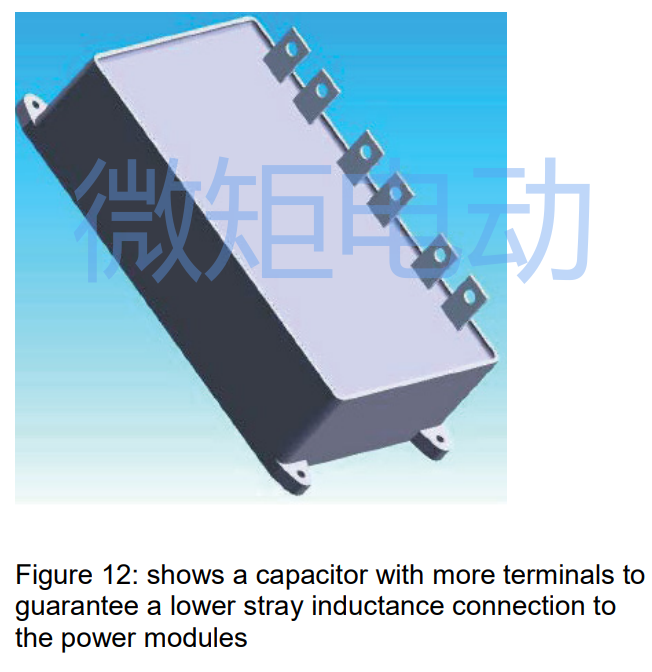
另外,在这个电容器的端子设计中端子之间的距离过大,将产生一个额外的电感。SiC 芯片的开关速度非常快,每一个nH的减少都将有助于以减少过电压。
eMPack已经提供了非常低的杂散电感,但如果电容器的连接不匹配,这就不能使用。
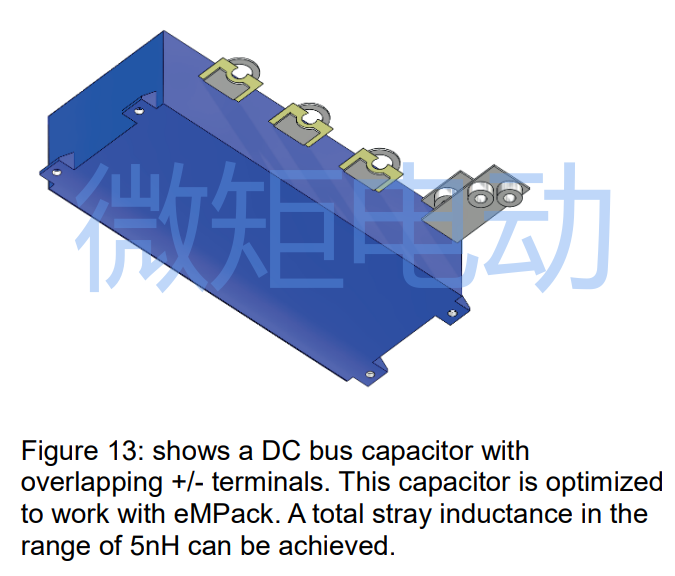
eMPack是一个用于最新芯片技术的功率模块。eMpack是未来的封装技术,可快速开关的功率器件,许多汽车公司中已经在试应用。
图14显示了一个紧凑的电气逆变器设计。500kW仅6升的体积。
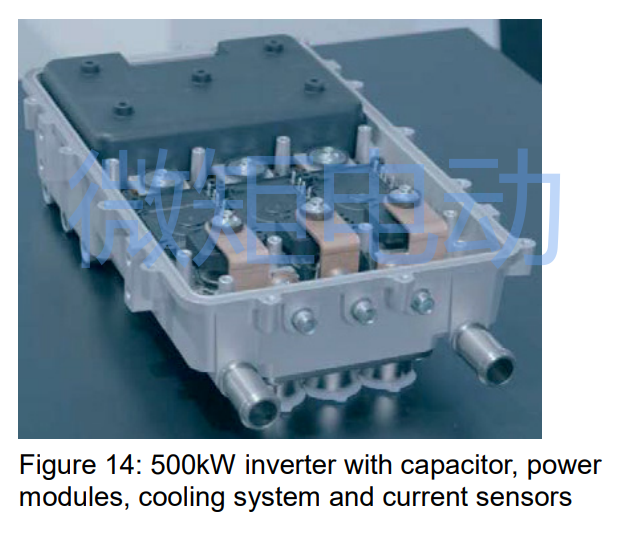
总结
封装技术将是未来WBG器件的最大挑战。为了保证WBG器件的全部性能,优化DCB和功率端子设计是必要的。大批量的生产需要优化的装配工艺。引入的可焊接端子是未来的正确方向。
这篇是PCIM上Semikron发布的paper,Semikron在模块封装上还是有很多独到之处。极致的低杂散电感对于SiC性能的发挥至关重要,如何减少整个功率回路的杂散电感涉及到功率模块封装,电容layout,电容和功率模块的连接,Semikron的这个方案整个主回路杂散电感可以做到小于10nH,是目前看到的最极致的设计。
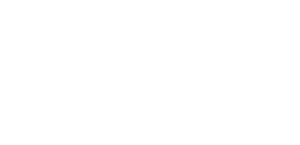
原文始发于微信公众号(微矩电动):铜排焊接的低杂散电感汽⻋级SiC模块