量产的质量稳定性是现代制造业的一个重要诉求,统计过程控制(Statistical Process Control, 简称SPC)在其中广泛应用,其目的就是建立并保持生产过程处于可接受的并且稳定的水平,以确保产品符合规定的要求。半导体产业尤其是SPC应用典型的行业,因其工艺精度要求较高且产量较大。
SPC是过程控制系统 (PCS,Process Control System)的一个高阶应用。在制造过程中,过程控制无处不在,生产设备会装备有各种检测传感器,可以获取许多测量值,如压力、流速、密度、酸度、速度、速度、压力、温度和重量等,设备或工作人员可以根据这些数据反馈对当前的工艺状态进行及时调整。然而工艺整体基准发生偏离的话,则很难为人所觉察。
而SPC借助数理统计的方法对生产过程进行分析评价,能很好的反映系统性因素导致基准偏移的问题。技术操作人员可以根据相应的失控(Out Of Control, OOC) 信号采取措施消除影响,使过程维持在仅受随机性因素影响的受控状态,以达到控制质量的目的。在先进封装中,SPC既是质量管理体系的核心工具之一,也是ISO认证审核的重要一环。
1924年,美国的贝尔电话实验室的休哈特博士提出将3 Sigma原理运用于生产过程当中,并发表了著名的控制图法,对过程变量进行控制,为统计质量管理奠定了理论和方法基础。
SPC主要解决两个基本问题:一是过程运行状态是否稳定,二是过程能力是否充足。前者可利用控制图这种统计工具进行测定,后者可通过过程能力分析来实现。故SPC还是一种以预防为主的质量控制方法。典型的SPC图表如下:
图1. SPC控制图(Control Limit-UCL通常为Center Line +/- 3 Sigma,基于正态分布)
第二类:数据点虽在控制界限内,但是排列的形状有缺陷,如准则2-8。
准则2:2/3A(连续3点中有2点在中心线同一侧的B区外<即A区内>)
准则3:4/5C(连续5点中有4点在中心线同一侧的C区以外)
准则5:8缺C(连续8点在中心线两侧,但没有一点在C区中)
准则8:15全C(连续15点在C区中心线上下,即全部在C区内)
先进封装中常见的KPP (Key Process Parameter) 及在SPC中的应用
首先是要确定KPP。通常工艺参数繁多,某个参数是否与最终的输出结果有显著联系,需要工程师基于原理或实验来验证,否则无效的参数会导致资源的浪费。对基于基板(Substrate)的先进封装,关键步骤包括晶圆切割,助焊剂喷涂,贴片,回流,助焊剂清洗,点胶,置球等环节,每个步骤都会有若干KPP。我们以贴片和回流详细展开。
贴片最主要的参数就是芯片相对于基板的位置偏移,包括X,Y,Theta以及TouchDown_Force_ Max (最大贴片压力)。其中位置偏移会导致焊点桥接(Bridge)或断路(Open),而最大贴片压力过大可能导致芯片断裂。
信号检测及统计量实现过程:贴片机的贴装头需配备有压力传感器,并且设备软件需要支持提取最大压力值;贴片完成后需要有AOI设备对芯片位置偏移进行检测。检测值上传到SPC系统后,基于一定样品量,该系统会根据预设的目标值(Target)和控制线(Control Limit)计算出各种统计量,比如OOC% (失控率),CpK (过程能力值),OTI (On target indicator,目标符合指标)等等。如图4,贴片机的X方向偏移数据,SPC将计算出相应的统计量,该图所反映的设备准确度不错,但精度可能不足。
SPC失控的触发(Trigger):一个批次(Lot)处理完成之后,如果数据有异常,SPC系统会阻止该批次执行结束指令。
SPC失控的响应:通常SPC系统会集成响应流程(RFC,Response Flow Chart),生产人员需要根据流程指令逐步处理,若非操作相关的问题,RFC会要求操作人员联系技术人员进一步解决。
SPC工程师的职责:基于统计指标设置合理的控制线,否则会导致失控(OOC)误报警(Over Alarm)或不报警(Under Alarm);通常要基于过去一周或数周的数据进行分析判断;检查RFC是否仍然有效,若无效则及时改进;审核一线操作人员对SPC触发的响应执行度,若执行度不足,需要及时报告给生产主管。
信号检测实现过程:在回流炉加装温度检测系统,比如KIC公司的标准测温仪,其在炉子进口和出口处有探测头以检测工件来料和出料情况,在炉子内部有测温线缆,每隔几厘米就有内置温度传感器,这样可以得到工件在炉内移动过程中温度随时间的曲线,如下图。
KPP选择:最高温度(Peak),液化温度时长(Time Above Liquid),升温速率(Ramp Rate)。其中升温速率可能会分阶段选取,比如50度~120度的速率,120~200度的速率等等。
同理其他工艺环节亦有相关的SPC系统配置,主要差别在于KPP的选择。比如晶圆切割环节切割边距偏移量,助焊剂喷涂环节中助焊剂的喷涂量,点胶环节胶量的爬坡程度等等。
问题来了,回顾之前的文章:TCB (热压键合)工艺,大家可以一起思考下相应的KPP该怎么选择呢?小提示:TCB贴合过程会大致分成6步。
另外还有一种控制图方法:EWMA (指数加权移动平均值) 在先进封装中亦有应用。该方法会将历史数据加权后累加到当前值,越靠近当前时刻的历史数值加权系数越大(参考文章: https://www.cnblogs.com /jiangxinyang/p/9705198.html)。
相较于传统的休哈特控制图,EWMA控制图有历史记忆能力,可以实现超前预报,对长期的小幅度工艺均值漂移有比较好的敏感性,可以弥补休哈特控制图的不足。比如某些生产环节对温度或压力漂移比较敏感的,可以采用该控制图来预测。SPC工程师要根据工艺特点设置合适的加权系数初始值。如果大家有兴趣的化,后续可以再开一篇文章详述。
在SPC实践中,我们要区分过程受控和加工结果规范的区别,虽然SPC的目的是通过控制加工过程来得到可期望的加工结果,但如果将生产过程统计受控与加工结果是否规范等同起来,则是一种不正确的认识。
SPC虽然是一种很有效控制工具,但考虑到该系统有一定的复杂性和门槛性,滥用SPC也是得不偿失的。
先进封装在逐步向晶圆级封装靠近的过程中,SPC的应用会越来越深入,而这正是先进封装迷人的地方之一。
原文始发于微信公众号(艾邦半导体网):SPC (统计过程控制)在先进封装中的应用
先进封装设备类似前道晶圆制造设备,供应商受益先进封测产业增长。随着先进封装的发展,Bumping(凸块)、Flip(倒装) 、TSV 和 RDL(重布线)等新的连接形式所需要用到的设备也越先进。以长球凸点为例,主要的工艺流程为预清洗、UBM、淀积、光刻、焊料 电镀、去胶、刻蚀、清洗、检测等,因此所需要的设备包括清洗机、PVD 设备、光刻机、 刻蚀机、电镀设备、清洗机等,材料需要包括光刻胶、显影剂、刻蚀液、清洗液等。为促进行业发展,互通有无,欢迎芯片设计、晶圆制造、装备、材料等产业链上下游加入艾邦半导体先进封装产业链交流群。
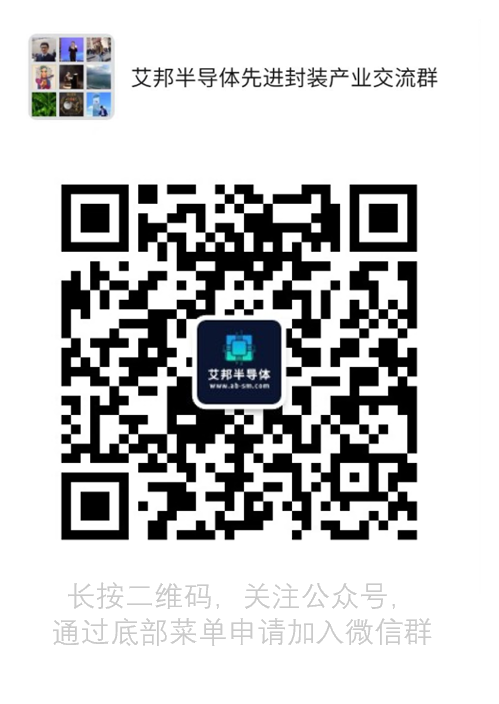