随着功率模块应用领域的不断扩展,要求功率模块具有更高的性能。为了满足市场需求,开发对功率模块的寿命、封装尺寸和功率密度有着极大影响的先进布线技术至关重要。楔形Al引线绑定技术作为传统方案被广泛应用,但是采用这种方案的模块寿命主要受芯片上引线绑定结疲劳寿命的影响,而且引线绑定区域通常会限制封装尺寸进一步减小。为了解决这个问题,三菱电机开发了全新的内部布线技术,如将新型布线材料及直接端子绑定技术(DLB:Direct Lead Bonding)应用于盒式封装模块。
摘要
1.简介
功率模块已经在家用电器、工业、汽车、铁路等领域中广泛应用,不同应用领域要求功率模块具有更长的使用寿命、更紧凑的尺寸或更高的功率密度。在开发新产品时,选择有利于上述性能的关键布线材料或方案是成功的主要因素, 如采用最近开发的Al合金线、Al-Cu包层线和Cu线等新型绑定线材料以提高模块寿命和功率密度。三菱电机开发了DLB技术来替代楔形线绑定技术,通过将主端子直接连接到电极,从而实现了高紧凑性和高可靠性,本文将对面向于下一代产品并专注于布线技术的封装技术进行介绍。
2.楔形线绑定技术
2.1 Al线
由于布线设计中灵活性高,楔形Al线绑定技术已广泛用于传统功率模块内部布线中,但是这类功率模块的寿命通常取决于芯片上引线绑定结的疲劳寿命。由于半导体芯片和Al线之间的热膨胀系数(CTE:Coefficient of Thermal Expansion)不匹配,热应变导致结产生形变并致使裂缝扩展,同时也受到由散热路径退化所导致热阻增加的影响。尤其是半导体芯片和基板之间焊接层的退化会导致热阻增加,从而加速导线结处的裂缝恶化并缩短疲劳寿命[1],最终将使Al线从芯片表面剥离下来。
为防止焊接层退化,如第3.1节所述,我们根据压注模封装功率模块(T-PM)相关开发理论,将封装材料中的硅凝胶改为硬质树脂,再封装成盒式模块,图1和图2分别给出了三菱电机传统盒式封装IGBT模块和第7代NX系列IGBT模块的横截面图。通过快速热循环测试评估了硬质树脂封装对芯片下方焊接层的影响。
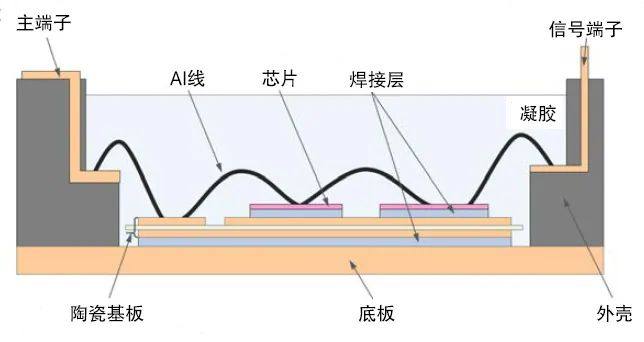
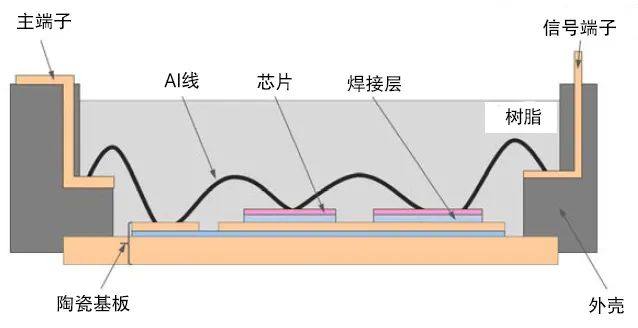
图3所示测试样品的结构中包括半导体芯片、Cu基板及这两个部分的相关焊接层。快速热循环测试的温度波动范围为+85↔+175℃。该实验可等效于功率循环测试的应变并可以模拟功率循环测试而无需半导体芯片动作。快速热循环测试完成后,对芯片贴装焊接层进行声波断层扫描(SAT:Scanning Acoustic Tomography)的结果如图4所示。
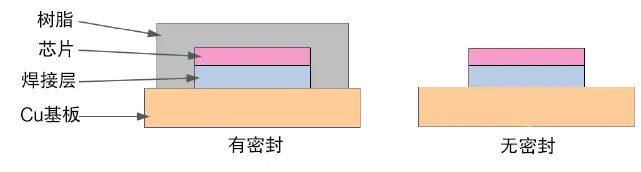
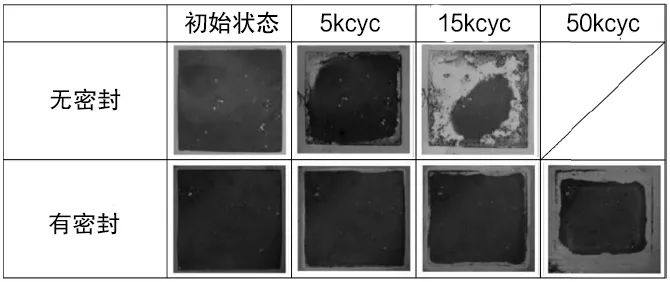
与无密封的样品相比,采用树脂密封后的样品能够有效防止裂缝扩展。试验结果表明,通过将硅凝胶改为硬质树脂可以缓解半导体芯片拐角周围的热应变,因此可以防止焊接层退化并提高Al绑定线的疲劳寿命。此外,使用绝缘金属基板(IMB:Insulated Metal Baseplate)可以减少基板之间的焊接层数量,从而最大程度地降低热阻的恶化。
2.2 增强型Al合金绑定线
与Al线相比,具有较高机械强度的Al合金线有望改善引线绑定结的疲劳寿命。表1中列出了用于快速热循环测试(+50↔ +150℃)的绑定线和电极材料组合,以评估应用Al合金线改善疲劳寿命的效果。
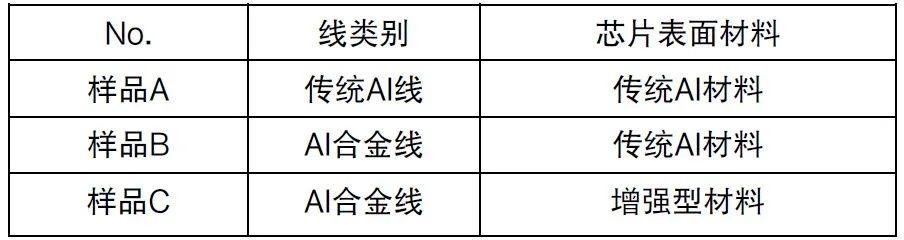
用于该测试的样品内置了陶瓷基板、通过焊料附着在基板上的半导体芯片以及粘结在半导体芯片和基板上的Al或Al合金线。快速热循环试验后每个样品的剪切强度的相对退化率如图5所示。
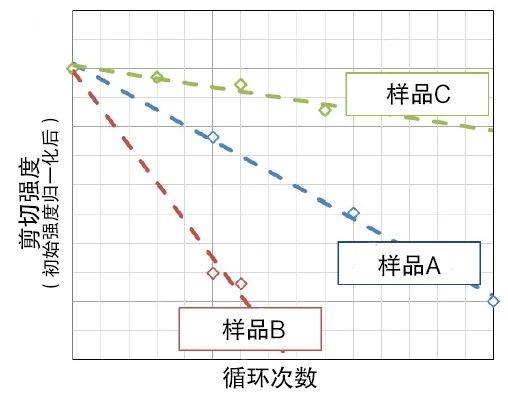
测试结果表明,仅将Al合金线应用于当前结构并不能很好地防止裂缝扩展到引线绑定结。图6给出了快速热循环测试后,引线绑定结处的截面放大后的扫描电子显微镜(SEM:Scanning Electron Microscope)图像。
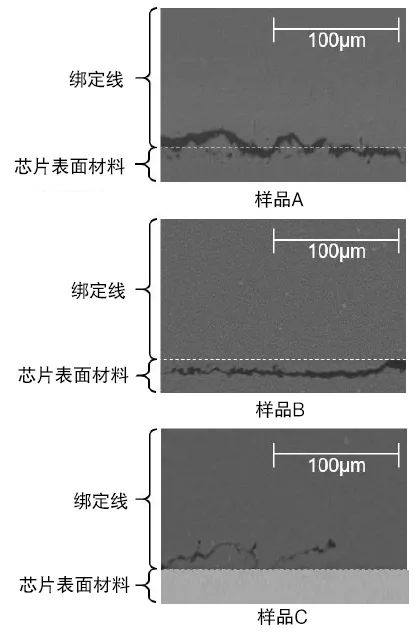
相比于样品A,样品B中的裂缝选择性地分布在芯片表面材料中。在样品B中,由于其导线的机械强度较高,杨氏模量与芯片表面材料的差异较大,导致芯片表面材料处应变集中增加并加速裂缝扩展。样品C通过采用具有较高机械强度的增强型线材料来替代传统Al线,能够有效缓解芯片表面材料处的应变集中。将Al合金线材与增强型芯片表面材料结合使用可有助于改善引线绑定结的疲劳寿命。
2.3 Cu线
与Al线相比,Cu线具有更高的重结晶温度及热膨胀系数与半导体芯片的更接近等特点,能够有效改善功率模块寿命。此外其更高的电导率能够提高功率密度或减少绑定线数量。但是将Cu线直接与Al电极接合具有一定难度,因此采用额外的厚金属涂层作为电极或在电极上附着缓冲层是Cu线绑定中的常规方法。图7给出了使用Cu线进行功率循环测试(+85↔+ 200°C)样品的内部结构示意图。
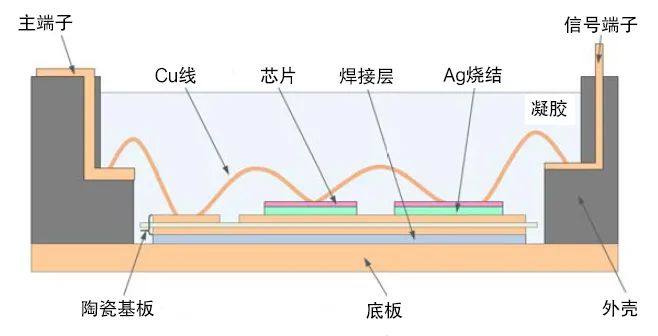
应用Ag烧结技术对图1中传统结构样品进行芯片贴装以防止芯片和基板之间的焊接层脱落,同时在半导体芯片电极上涂有较厚的电镀金属层。在参考样品中,Al线绑定在常规Al电极上。通过对2个样品进行测试对比,使用Cu线绑定的模块比用Al线绑定模块的PC寿命提高37倍,如图8所示。
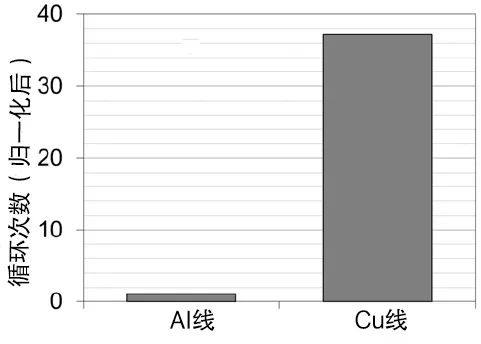
如上所述,在使用Cu线时有必要在半导体芯片上采用厚金属化或缓冲层之类的保护结构。此外,通过应用Cu线显著改善引线绑定结的疲劳寿命有时会导致其他关键失效模式[2],因此为了实现充分利用Cu线的优异性能,仅仅只是采用Cu线是不够的,还需要对整个封装结构进行优化。
3. 直接端子绑定技术(DLB)
3.1 针对压注模封装模块的DLB技术
如图9所示[3],我们首先将DLB技术应用于压注模封装功率模块J系列T-PM的设计中。压注模封装模块采用DLB结构能够有效提高可靠性,这得益于其与芯片连接面积加大且压注树脂能够有效降低焊接层上的应变集中。
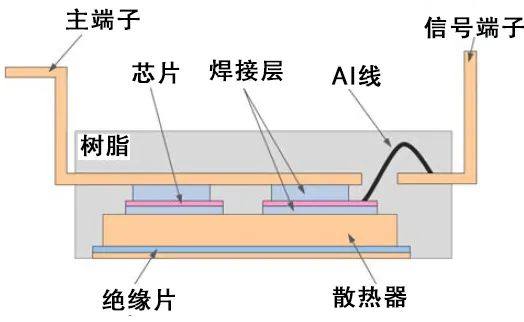
Al引线绑定模块和DLB T-PM之间的功率循环(PC:Power Cycling)寿命比较结果如图10所示,其中DLB T-PM可以将PC寿命提高到Al引线绑定型T-PM的10倍以上。仿真结果再次确认了大面积焊接连接使芯片表面温度均匀分布,而在芯片内部没有出现任何电流集中,如图11所示。温度均匀性除了能够提高使用寿命外,还有助于增加电流密度,DLB可以减小基板上引线绑定面积来进一步缩小封装尺寸。
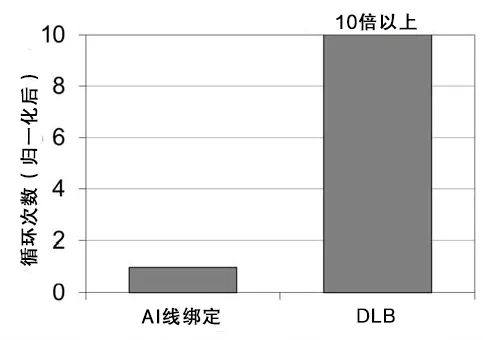
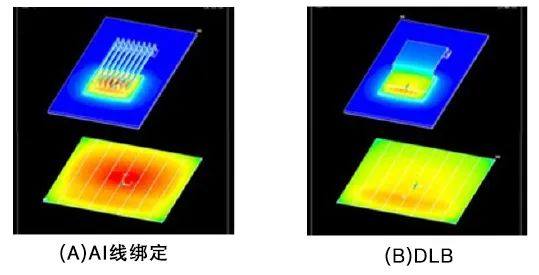
3.2 针对盒式封装模块的DLB技术
通过将DLB技术应用于盒式封装模块,三菱电机已经开发出了用于电动汽车的J1系列IGBT模块,如图12所示[4]。
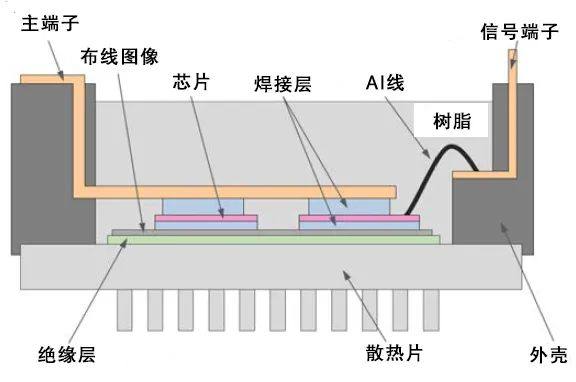
为了成功将DLB技术应用于盒式功率模块,我们同时也开发了DLB和环氧树脂结合的封装组合。在DLB结构中,控制连接部分上的焊料形状是有效提高寿命效果的重要因素之一。但是将DLB技术应用于大型盒式模块中时,由基板翘曲导致的主端子与芯片表面之间的间隙距离成为问题。
另外,从固定端到主端子前端连接部位的距离变长,间隙的偏差也变大。在主端子上形成通孔对于控制焊料形状和稳定可靠性十分有效,具体如图13所示。在间隙狭窄的情况下,焊料会扩散到通孔中以防止熔融焊料从芯片电极的边缘溢出。在另一种间隙较宽的情况下将自动调整通孔处的焊料形状,以充分确保焊料覆盖所需区域。
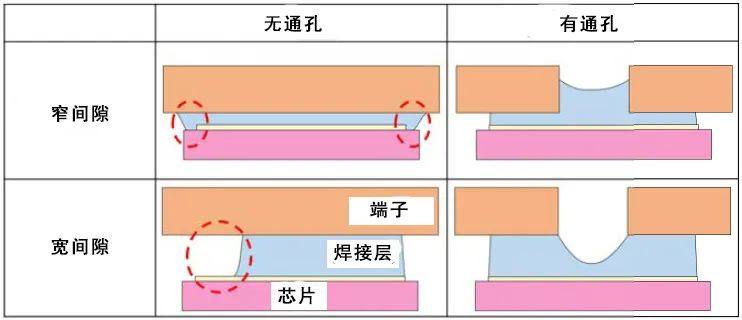
3.3 直接功率板绑定技术
如图14所示,通过不断地发展当前DLB技术已经可以做到主功率板直接绑定[5],其中功率板与半导体芯片电极直接连接且在其绝缘层正面和背面都设有较厚导电层。这类功率板设计为能够在单板中实现主功率布线和信号布线。通过使用多层功率板可以进一步缩小功率模块体积。通过设计图像布局,不仅可以利用正面层和背面层之间的互感来减小寄生电感,还可以降低并联芯片中的电流不平衡性和开关时间延迟,且这种新型3D互连设计可以应对未来的复杂拓扑。
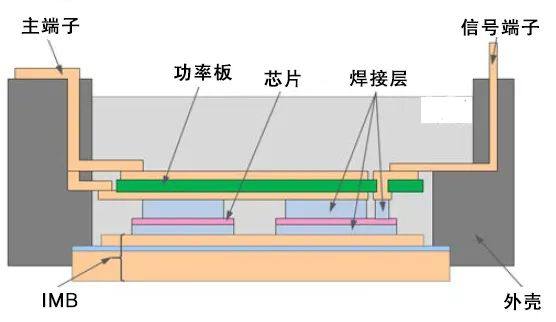
4.结论
全新布线技术已成功实现了对功率模块可靠性和小型化的改进,Al线与树脂封装、Al合金线和具有较高机械强度的增强型电极相结合可以有效提升功率模块使用寿命。为了利用具有更高可靠性的Cu线,必须考虑整体封装结构改进,其中应用具有最佳焊料形状的DLB技术,不仅可以提高可靠性,还可以改善大型盒式封装模块的电气特性。布线技术的不断发展有助于实现针对广泛应用领域的新型功率模块。
原文始发于微信公众号(三菱电机半导体):【论文】针对下一代功率模块的布线技术
为加快产业上下游企业交流,艾邦建有IGBT产业链交流,欢迎识别二维码加入产业链微信群及通讯录。
长按识别二维码关注公众号,点击下方菜单栏左侧“微信群”,申请加入群聊