01
SiC mosfet 和Si IGBT 的性能对比
在探讨新能源车的牵引逆变器功率器件首选是SiC还是Si 器件之前,我们先简单对比SIC MOSFET 和 IGBT 基本特性。
-
在电流较小时,SiC mosfet 具有更小的导通损耗 -
当电流较大(超过曲线交点)时,IGBT 的导通损耗则更小
图 1 IGBT 和SIC MOSFET导通特性
图片来源:英飞凌
从开关特性看,IGBT属于双极性器件,在关断时由于少子的复合肯定会造成拖尾电流,使其开关损耗特性较差。而SiC MOSFET具有更快的开关速度,且没有拖尾电流, 所以其开关损耗对比IGBT具明显优势。
图 2 IGBT 和SIC MOSFET开关特性
图片来源:英飞凌
综上,SiC MOSFET器件并不是在所有负载条件下,都具有压倒性的性能优势。这也就很容易理解在选择SiC mosfet 还是Si IGBT 时需要考虑一个盈亏平衡点。
了解了SiC mosfet 和Si IGBT 的应用特点,针对不同的动力构型,我们应该如何选择呢?想要回答这个问题,我们先要了解:目前的动力构型有哪些?以及,在标准驾驶循环中究竟需要什么样的功率特征?
02
新能源车动力配置布局
新能源电动汽车的性能分配有多种选择,主流方案就是在主驱动轴和副驱动轴之间进行分配。如下图3所示,主驱动轴始终处于啮合状态,满足低功率常规续航驾驶模式,副驱动轴可提供额外扭矩,实现四轮驱动能力和最佳加速性能。当前市场上可以看到的配置基本分为:
1) 主驱动轴和辅驱动轴均采用了SiC功率器件;
2)主驱动轴采用高性能SiC功率器件,而辅驱动轴则采用更具性价比的IGBT功率器件。
这也是当今电动汽车的典型配置,这些方案均是建立在逆变器中使用单一的功率器件,较难做到效率和成本之间的平衡。在评估上述方案的优劣之前,我们需要先从电动汽车的驾驶工况来分析。真实的驾驶工况对牵引逆变器的需求是什么?
03
标准驾驶工况WLTP 与峰值性能需求
标准驾驶循环工况:WLTP
全球轻型汽车测试程序(WLTP)的驾驶周期反映了接近真实的驾驶任务。通过标准化,它为电动车制造商和消费者提供了比较不同车辆效率的参考值。对于电动汽车来说,它以一定距离的能量消耗来表示,比如100 公里消耗10 千瓦,或者以"每加仑汽油当量英里数"(MPGe)来表示,这一指标也可以与传统内燃机汽车进行比较。
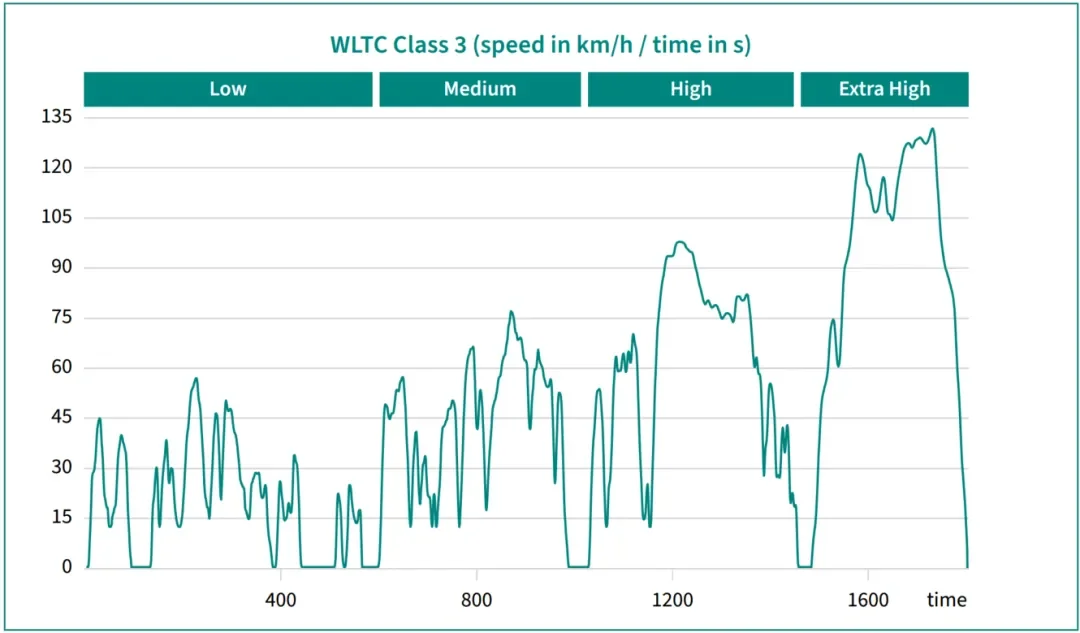
| SysPro备注:
按工信部要求,中国于2020年开始正式执行适合中国工况的标准CLTC驾驶循环。如下图所示,CLTC较原始NEDC而言,增加了范围更广的路况信息:城市工况、郊区工况和高速工况,循环时间仍与WLTP一致,为1800s;但是,相对于WLTP,缺少了超高速段的工况定义,且最高车速、平均车速为三者最低。
从上面的WLTP 典型的驾驶工况曲线来看,超过105km/h高速工况需求的时间占比大约只有10%左右,而大约3/4的时间内车速需求是小于75km/h。以一辆重1500 千克的汽车为例,计算出的数值绘制成直方图(图5)。该图表显示,电动车牵引逆变器的最大输出功率需要约50 KW。这说明对于电动汽车的加速、达到峰值速度所需的实际功率是非常小的。在发电模式下(见图5 中的紫色条),最大功率约为28 KW。
04
——Si还是SiC,主驱逆变器如何选择?
我们知道,牵引逆变器对电动汽车的整体性能和效率起着决定性作用。更仔细地审视逆变器的设计,成本效益和合理的额定功率以及合理的效率水平是面向更广泛市场的电动汽车取得成功的关键因素。在这个层面上,简单地说,我们要评估的是整个驱动任务剖面的最低性能和所需的峰值性能。从这个视角来看,到底哪种半导体技术(Si 或SiC)更适合呢?
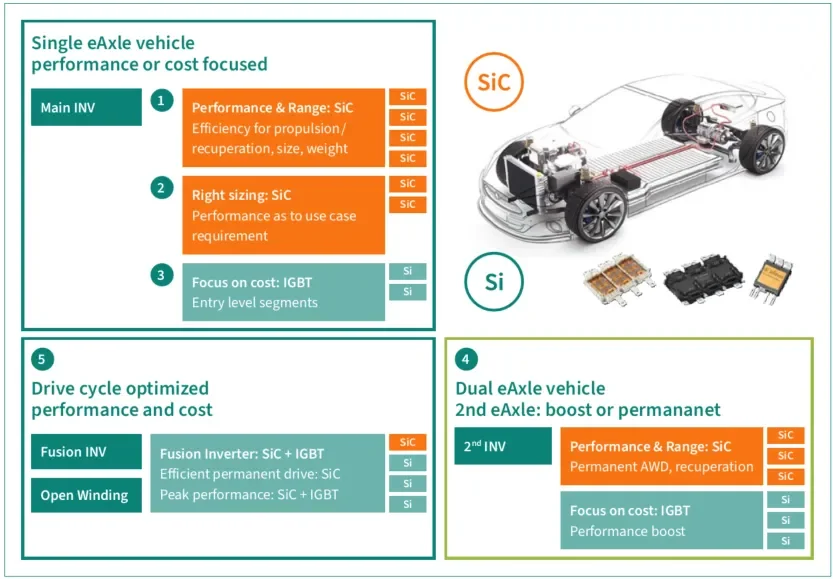
在前面的例子中,80 KW的电机可以执行标准的WLTP 驱动循环,从而满足大多数驾驶要求。如果使用碳化硅来提高汽车的额定功率,那么多余的功率在大多数情况下都会被"闲置"。但是在某些情况下,80 KW可能不足以实现"有趣动感"(运动型)的驾驶体验。因此,可以添加一些SI来提高车辆的峰值性能。例如,SI部件能够额外提供160 kW的功率。这将使汽车具有非常动感的驾驶加速性能。在另一方面,这些数值可以缩减到40 kW SiC 和80 kW Si,从而实现120kW 的入门级电动汽车功率。
| SysPro备注:英飞凌提的这一点确实如此,在追求低成本的今天,没必要花很大的代价在主驱上一味的追求高功率,并且主驱是长时工作动力系统,大功率去配一个低路面负载,无法把系统效率的最佳能力发挥出来。与其如此,不如选择一个小功率同步主驱+备用功率异步辅驱的构型,根据不同场景下的负载需求,适时执行2驱/4驱的切换。将对的东西用在对的场合。
4.2 不同动力构型下,Si还是SiC?
对于动力传动系统,尤其是牵引逆变器,不同的技术方案具有不同的效率、性能和成本优势,如下1~5配置:
-
单电驱,高性能和长续航要求 -> 大功率SIC逆变器
-
单电驱,适当调整车辆性能 -> 小功率sic逆变器
-
单电驱,成本优化的解决方案 -> IGBT逆变器
-
双电驱,高性能和长续航要求 -> SIC逆变器作为主驱续航,IGBT 逆变器作为辅驱提供加速动力
-
新型电驱,成本优化,高性能和长续航要求 -> 单逆变器中融合SiC+IGBT,SiC维持高效率续航运行,SiC+IGBT 提供峰值搞性能
下图展示了双电驱系统的设计初衷,结合SIC/SI IGBT的特征,我们直到:SiC在中小功率等级使用时具有更低的损耗、更高的效率,而IGBT在大功率输出时相对更有优势。为了充分发挥SiC和IGBT 各自的优点,双电驱可以采用不同半导体器件进行搭配。在这种配置(图6中 配置2 + 配置3 的组合)中,使用了Si 和SiC 技术,但部署在不同的电驱上。
-
主驱使用SiC, 保持持续运行且覆盖90%以上的WLTP驱动周期。 -
辅驱采用IGBT,提供额外的扭矩,以提供4轮驱动能力和最大性能。
-
SIC小电流下低导通损耗+全范围较优的开关损耗 -
SI IGBT大电流下低导通损耗
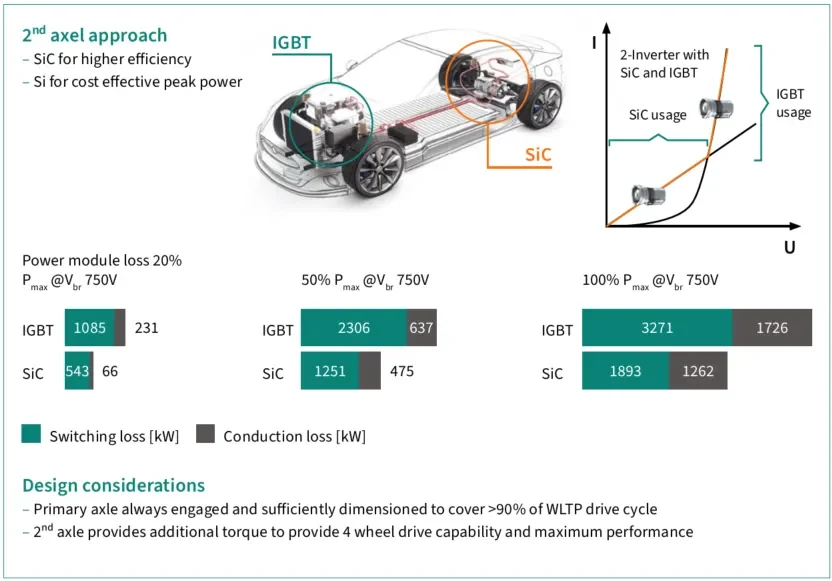
图片来源:英飞凌
05
Si和SiC融合技术?
-
配置1和2在后轴或前轴上使用了全部的碳化硅 -
配置3和4则使用了融合技术牵引逆变器。
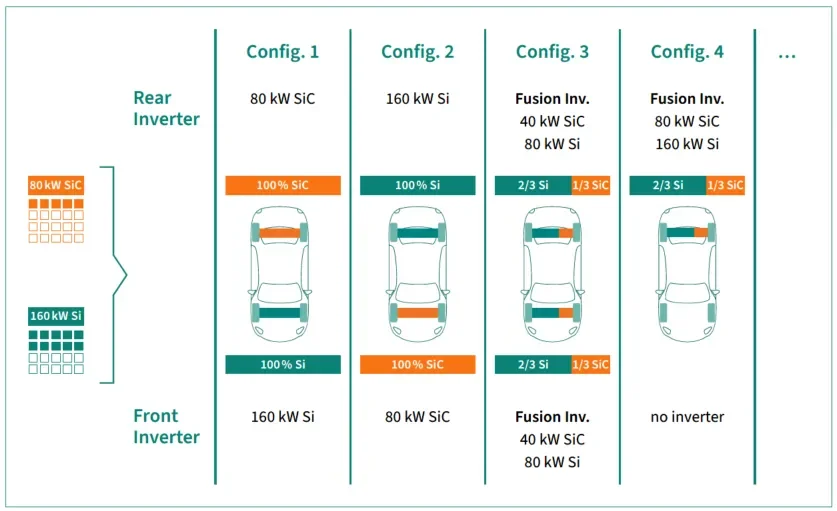
图片来源:英飞凌
下面我们聚焦融合技术,关注下SIC/SI融合技术在牵引逆变器中的能量流情况,如下图9所示。在标准负载下,后轴上的SiC 用于加速,而前后轴上的SiC(66% 至33% 的份额)用于平稳减速。这种负载情况与大多数驾驶条件和WLTP 测试条件相当,加速和减速完全由SiC 和所需的电驱控制。当功率需求达到更高峰值水平时,加速时需要使用额外的Si。由于Si在高负载时具有更高的效率,因此此处仅使用Si进行能量回收。
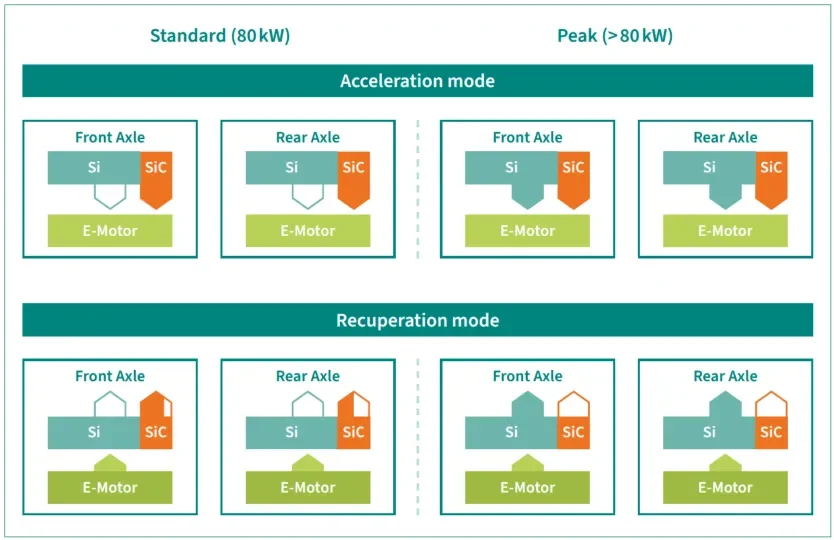
-
加速时候:在<80kw,只是主驱SIC介入 -
加速时候:在>80kw,需要后备力量,辅驱SI+主驱SIC -
减速时候:在<80kw,一部分SIC介入就够了 -
减速时候:在>80kw(很少出现这种情况),只是辅驱SI介
总而言之:融合技术牵引逆变器最有效地利用了不同半导体功率器件的不同优势,从而可以为高效、经济的电动汽车做出了的贡献。
06
在牵引逆变器中的应用
根据上述原理,这些技术可以通过不同的组合方式实现不同的目标。在只使用一种半导体技术的标准牵引逆变器中,由于只使用了Si 或SiC,因此不需要特别的驱动策略。但融合技术牵引逆变器采用了Si和SIC并联运行,因此也需要特殊的驱动控制策略。那么,如何考虑其驱动策略?
| SysPro备注:回答,如何考虑SIC/SI的驱动方式和路径?
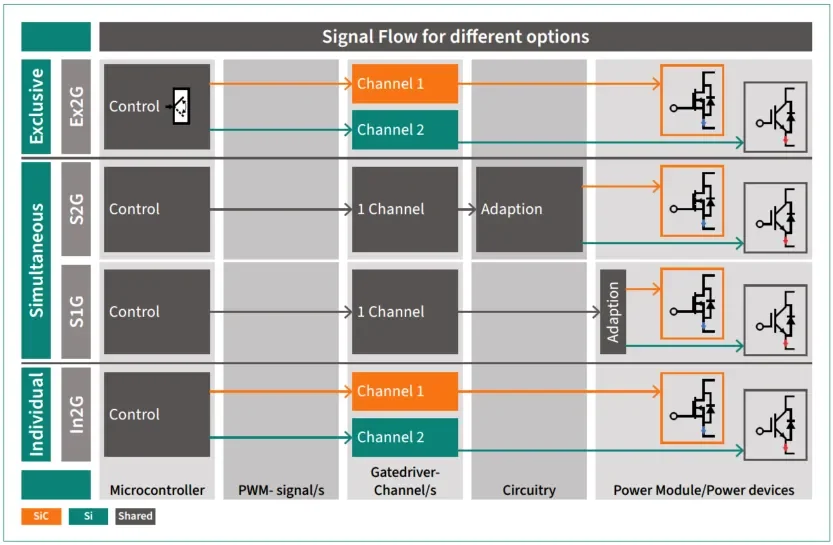
图10 融合技术的不同驱动控制策略
图片来源:英飞凌
方式1:独立运行("Ex")
方式2/3:并行控制("S")
方式4:单独控制("In")
单独控制模式需要两个栅极(In2G),因此设置更为复杂,但另一方面,它充分利用了融合技术牵引逆变器的优势。它还提供了两种技术之间的冗余(故障切换)。
07
不同的实施模式有何不同?
06中英飞凌分析了不同的融合技术牵引逆变器驱动策略的实现方法,使我们能够识别和比较这些不同。下图11 总结了每种实施方法的优势和挑战。
如图所示,每种控制策略在某些用例中都具有优势和缺点。合适的产品和工程能力往往决定了实施的可行性。基于这些边界条件,不同的细分市场将可以采用不同的融合技术牵引逆变器控制策略。
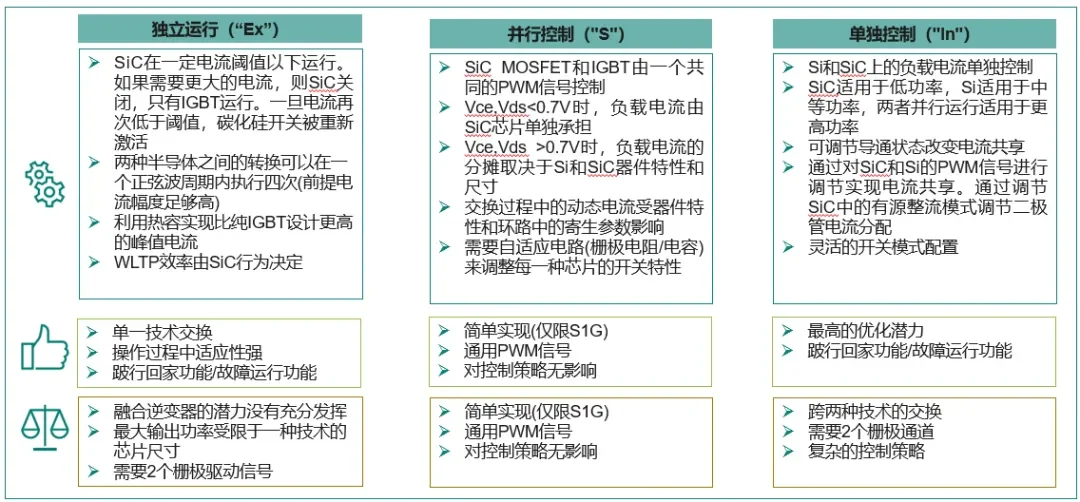
单独控制模式(In2G)是一个不错的驱动策略,因为它具有充分的灵活性,为高度复杂的软件策略打开了大门,可优化不同半导体开关技术的电气效率、BOM、成本和使用寿命等变量。这种模式甚至可以支持"故障运行"功能。因此,融合技术牵引逆变器的优势不仅限于最初明显的成本和材料可用性优势,还能为未来的新能源汽车提供新的技术方向。Si和SiC融合技术将是一种非常有效的解决方案,可以瞄准需要在效率、成本和可用性之间取得良好平衡的细分市场。
08
英飞凌目前正在扩大其产品组合,以充分发挥融合技术在逆变器应用中的优势。从Si 和SiC 裸芯片到分立器件、功率模块,再到支持两种技术的混合模块,英飞凌的产品范围十分广泛。
英飞凌第一款750V Si/SiC 混合功率模块已经面向市场推广。英飞凌利用其最新Si和SiC芯片开关性能良好的匹配特性,第一款 混合功率模块可以采用常规单通道驱动模式,不增加系统控制复杂性 同时电控系统的性能可以获得提升。如下图所示,根据仿真175KW 400V BEV 电驱平台采用英飞凌混合模块对比采用纯IGBT模块,WLTP工况驾驶里程可以提高2.9% 。
图12 英飞凌混合模块
来源:SysPro系统工程智库
原文始发于微信公众号(武汉新瑞科):混合式SiC MOSFET+Si IGBT,如何在逆变器效率、成本、可持续性中找到最优解?