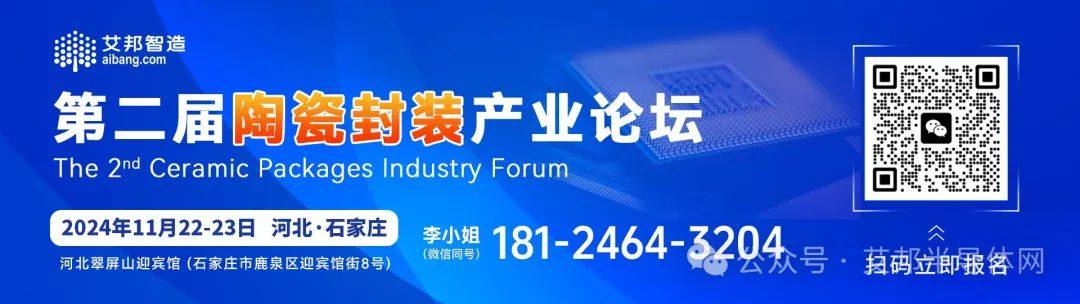
玻璃基板的出现满足了业界对人工智能等高性能应用的巨大需求及其严格的要求,包括进一步减小玻璃通孔 (TGV) 的尺寸和间距。到目前为止,有机基板采用镀通孔 (PTH) 型通孔,但这些通孔无法满足这些具有挑战性的要求。
随着玻璃芯基板取代有机基板的出现,迄今为止需要基本印刷电路板 (PCB) 技术的各种工艺都进入了新的阶段,复杂性显著提高。本篇讨论了基板中互连的形成,无论这些互连是有机基板的 PTH 还是玻璃基板中的 TGV。
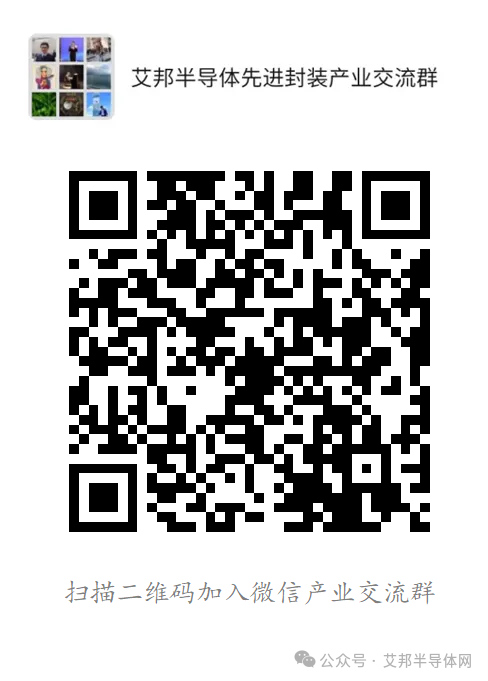
先前的 PTH 技术需要在覆铜板 (CCL) 基板上进行机械钻孔。这些孔的直径通常约为 0.2mm至 1mm。钻孔后,使用已有数十年历史的化学镀铜工艺对孔进行电镀。为了满足 AI 等先进封装的要求,PTH 将被 TGV 技术取代,该技术能够提供小于 0.1mm的通孔和更细的间距。
对于玻璃芯基板加工,创建 TGV 的最流行方法是使用激光,结合湿蚀刻工艺。目前,这些通孔通常是沙漏形;然而,一些制造商正在尝试圆柱形和 V 形。一旦制造出 TGV,它们将用铜填充,以提供玻璃面板基板正面和背面之间的电气连接。
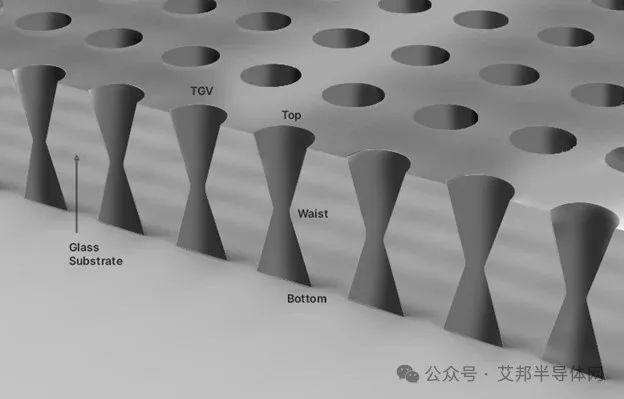
图1:带有玻璃通孔的玻璃基板的横截面图
但在所有创新中,仍存在一些工艺挑战,包括裂缝、划痕、通孔缺陷等。我们从最具挑战的问题开始讨论。
通孔临界尺寸 (CD) 控制:顶部、底部和腰部之间的 CD 关系控制侧壁角度,这在铜种子物理气相沉积 (PVD) 工艺中非常重要。由于 TGV 底部的凹角,面板必须在 PVD 腔内翻转,以确保完全覆盖种子金属。这些 CD 可以通过高速自动光学检测系统 (AOI) 确定,该系统能够在不到五分钟的时间内收集数百万个通孔的尺寸。值得注意的是,一些制造商正在使用粘合化学来继续化学镀铜种子沉积技术。这也会影响 CD 变化。
缺失或有缺陷的通孔:必须保证 100% 的 TGV 是开放的且无缺陷。通过将 AOI 的 TGV 位置与计算机辅助设计 (CAD) 布局进行比较,可以在数百万个通孔中找到一个缺失的通孔,这就像大海捞针。
镀铜填充、空洞、凹痕和凸起:使用 PTH 时,只需要在钻孔的孔壁周围进行镀层。然而,就 TGV 而言,行业目前正朝着两条不同的方向发展。虽然许多制造商选择用铜完全填充 TGV,但其他制造商只用金属镀层侧壁,然后用介电材料填充 TGV 的其余部分,类似于有机基板中的 PTH。声学技术能够检测填充物中的空洞,而干涉传感器可以在对铜填充覆盖层进行化学机械平面化 (CMP) 后确定凹痕和凸起的地形性质。
裂纹和划痕:进来的材料可能会出现裂纹和划痕,尤其是在面板边缘。在 TGV 中填充铜后,热循环也会在玻璃芯内产生应力裂纹。这会导致可靠性问题。此外,这些应力可能会导致裂纹在工艺的最后步骤中毫无征兆地扩散,从而对产量和最终产品性能产生负面影响。这尤其成问题,因为面板厚度预计将减少到 200µm。
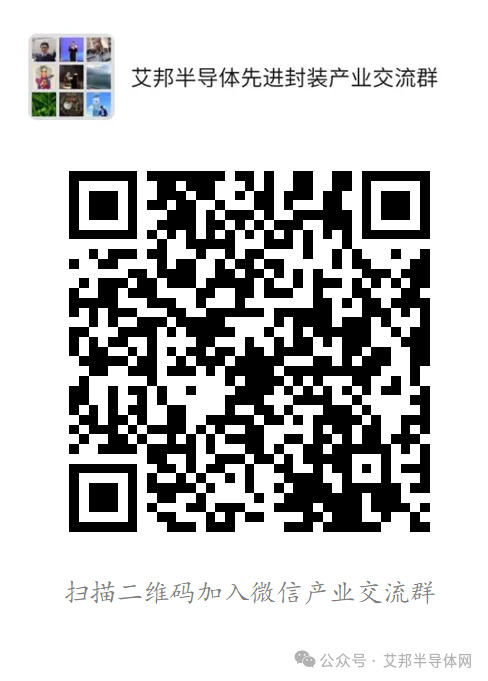
为了深入了解之前强调的故障机制,在 TGV 制造工艺的研发阶段,高速、100% 的检查至关重要。然后,使用试验线玻璃基板的统计监控,可以使用带有 AI 和机器学习算法的先进自动缺陷和分类 (ADC) 软件在工艺流程的早期识别致命故障机制并帮助防止裂纹扩展。这最大限度地降低了在最后工艺步骤中报废面板的昂贵风险。除了 TGV 缺陷检查外,还需要 TGV 计量来保持放置精度、圆度和 CD 控制。需要监控和控制所有关键参数以防止产量损失。
从缺陷预防的角度来看,自动化机器人基板处理、进来的玻璃面板质量控制和玻璃热膨胀系数 (CTE) 与其余封装组件的匹配,也在使玻璃芯基板更接近 HVM 准备方面发挥着重要作用。
将玻璃芯基板的线宽/间距 (l/s) 控制在 1.5µm 以下一直是许多工艺工程师的工作;您甚至可以称其为先进封装领域的珠穆朗玛峰挑战。现在的问题是,玻璃芯基板工程师需要多长时间才能实现高良率的 HVM TGV 工艺?
目前,许多人仍对是否有必要使用玻璃基板而非传统有机基板持观望态度。事实上,许多晶圆厂仍在推广有机基板,因为他们相信有机基板可以扩展到 1.5µm l/s。无论如何,对于本文中讨论的所有挑战,工艺控制 解决方案都是不可避免的。
在此之前,有机基板和玻璃基板将继续共存,各自达到新的技术高峰。最终,封装架构和/或制造成本将决定哪种技术首先达到这一新高峰。
为促进行业发展,互通有无,欢迎芯片设计、晶圆制造、装备、材料等产业链上下游加入艾邦半导体先进封装产业链交流群。
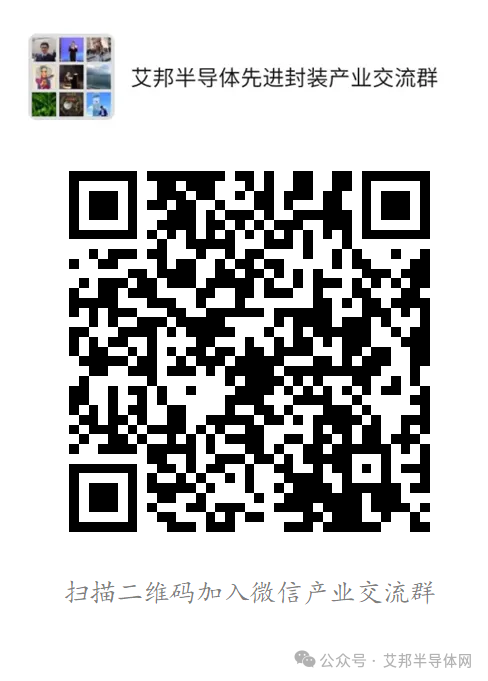
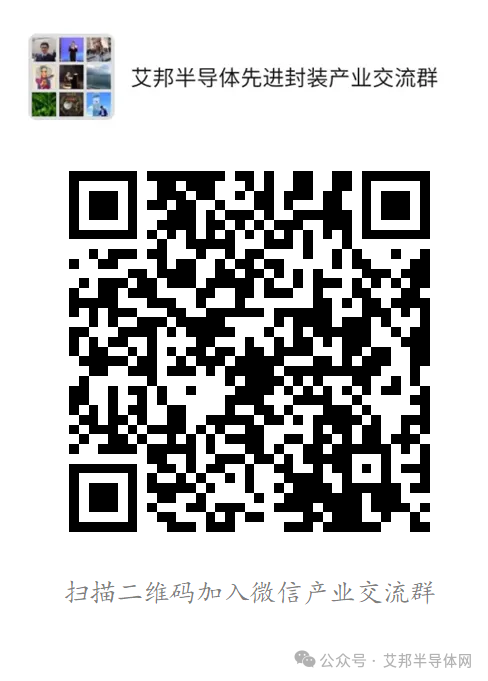
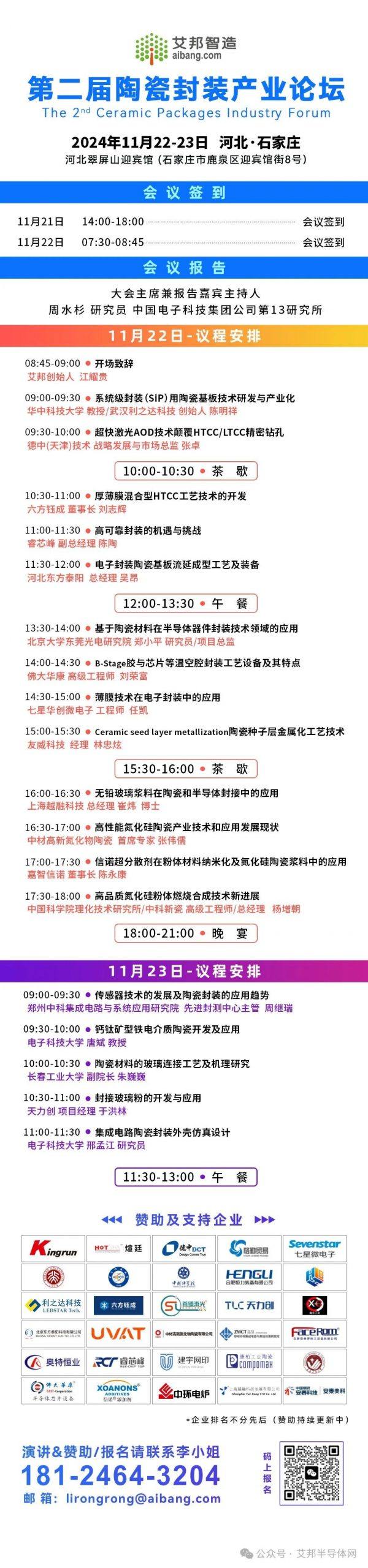
原文始发于微信公众号(艾邦半导体网):将玻璃通孔 (TGV) 引入大批量生产
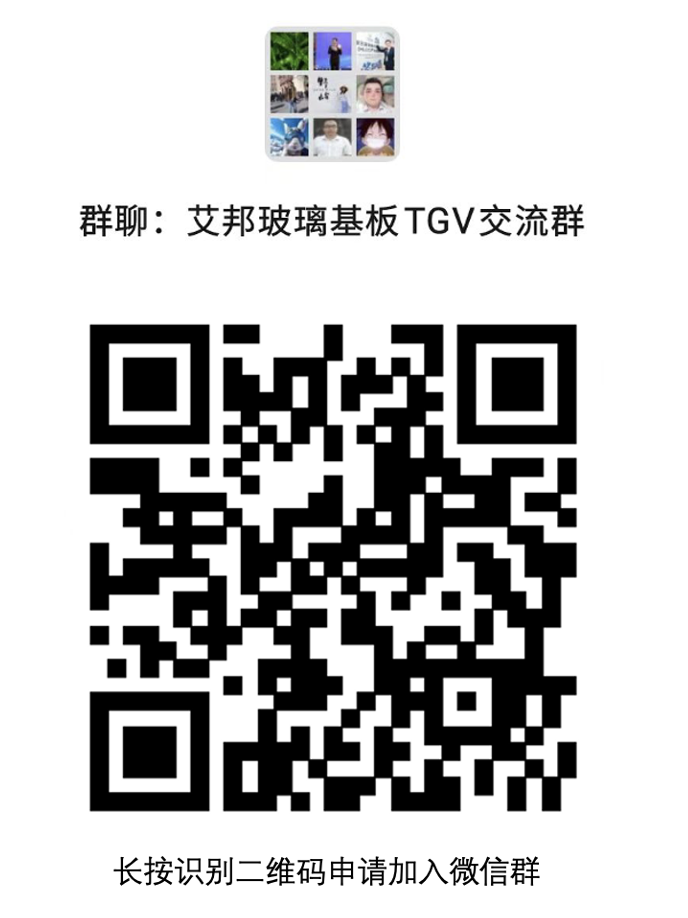