前期准备
激光打孔
蚀刻处理
通孔形成
后续处理
孔壁金属化
光刻
孔填充
基板表面平整
保护层及终端连接
资料来源:中科岛晶
应用终端 芯片设计 equipment wafer 检测设备 视觉 自动化 半导体 芯片 封装 芯片测试 material 设备配件 传动机构 清洗设备 化学品 Plastic 硅片 光掩膜版 磨抛耗材 夹治具 切割设备 激光设备 光罩盒 IC载板 载具 CMP抛光垫 光学元件 抛光液 模具 电子特气 蚀刻设备 光刻胶 靶材 塑料制品 耐酸碱 管道阀门 氟材料 光刻机 环氧塑封 特种塑料 涂层 耗材 晶体生长炉 热工装备 划片机 磨抛设备 化学机械抛光设备 离子注入设备 PVD 涂胶显影设备 等离子去胶设备 胶带 清洗剂 包装设备 包装 管路 抗静电剂 ceramics 元器件 碳碳制品 高校研究所 代理 贸易 其他 CVD 光源 胶水 载带 玻璃 有机硅 薄膜 密封圈
成员: 5306人, 热度: 153517
ceramics 天线 通讯 终端 汽车配件 滤波器 电子陶瓷 LTCC MLCC HTCC DBC AMB DPC 厚膜基板 氧化铝粉体 氮化铝粉体 氮化硅粉体 碳化硅粉体 氧化铍粉体 粉体 生瓷带 Ceramic substrate 氧化铝基板 切割机 线路板 铜材 氮化铝基板 氧化铍基板 碳化硅基板 氮化硅基板 玻璃粉 集成电路 镀膜设备 靶材 电子元件 封装 传感器 导电材料 电子浆料 划片机 稀土氧化物 耐火材料 电感 电容 电镀 电镀设备 电镀加工 代工 等离子设备 贴片 耗材 网版 自动化 烧结炉 流延机 磨抛设备 曝光显影 砂磨机 打孔机 激光设备 印刷机 包装机 叠层机 检测设备 设备配件 添加剂 薄膜 material 粘合剂 高校研究所 清洗 二氧化钛 贸易 equipment 代理 其他 LED
先进封装设备类似前道晶圆制造设备,供应商受益先进封测产业增长。随着先进封装的发展,Bumping(凸块)、Flip(倒装) 、TSV 和 RDL(重布线)等新的连接形式所需要用到的设备也越先进。以长球凸点为例,主要的工艺流程为预清洗、UBM、淀积、光刻、焊料 电镀、去胶、刻蚀、清洗、检测等,因此所需要的设备包括清洗机、PVD 设备、光刻机、 刻蚀机、电镀设备、清洗机等,材料需要包括光刻胶、显影剂、刻蚀液、清洗液等。为促进行业发展,互通有无,欢迎芯片设计、晶圆制造、装备、材料等产业链上下游加入艾邦半导体先进封装产业链交流群。
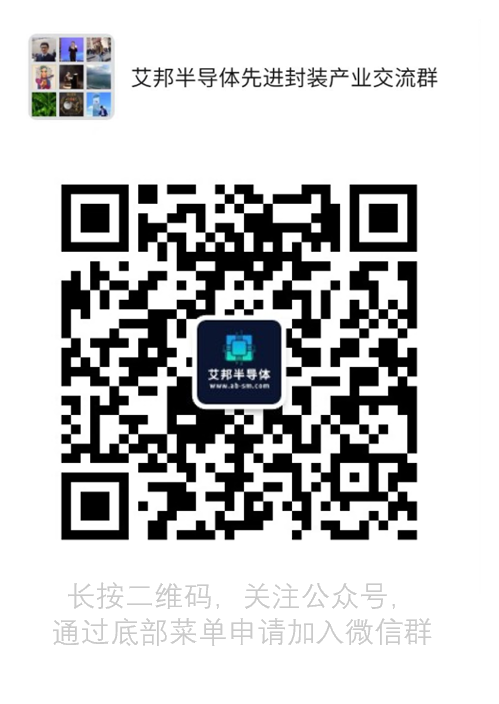
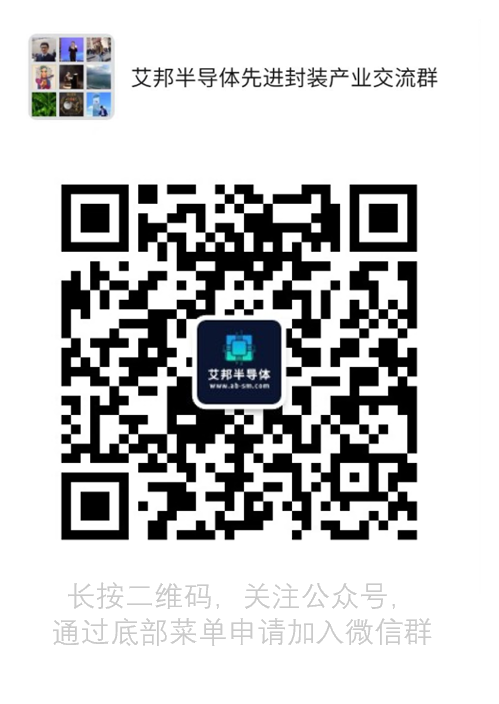
我们诚邀您加入“玻璃基板与TGV技术交流群”,与行业精英共同探讨玻璃基板及TGV技术的前沿动态,共享资源,交流经验。在这里,您可以第一时间获取技术革新信息,深入解析行业趋势,与行业领袖面对面交流,共同推动技术革新,探索无限商机。
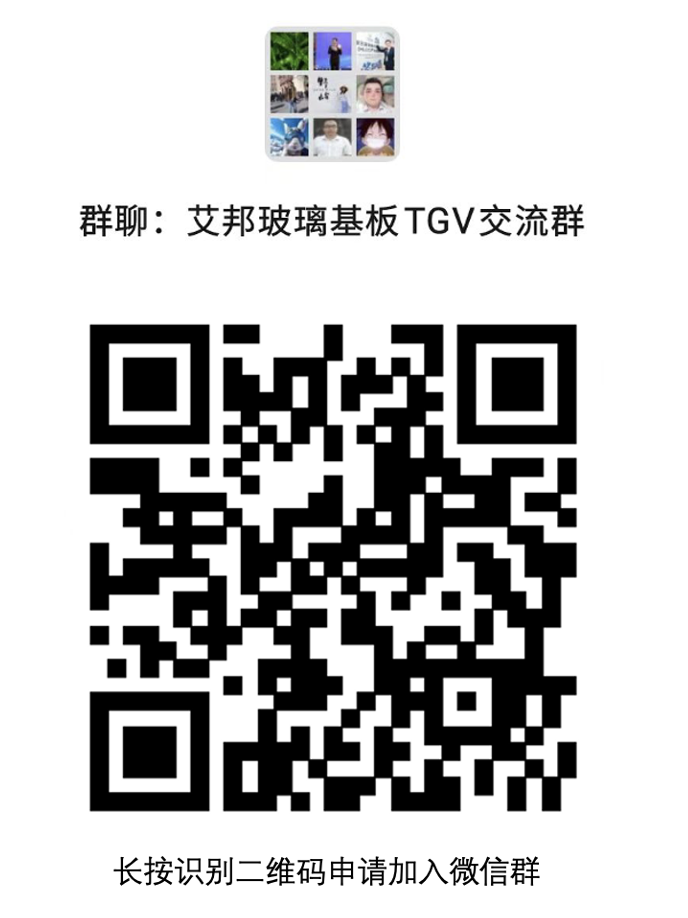
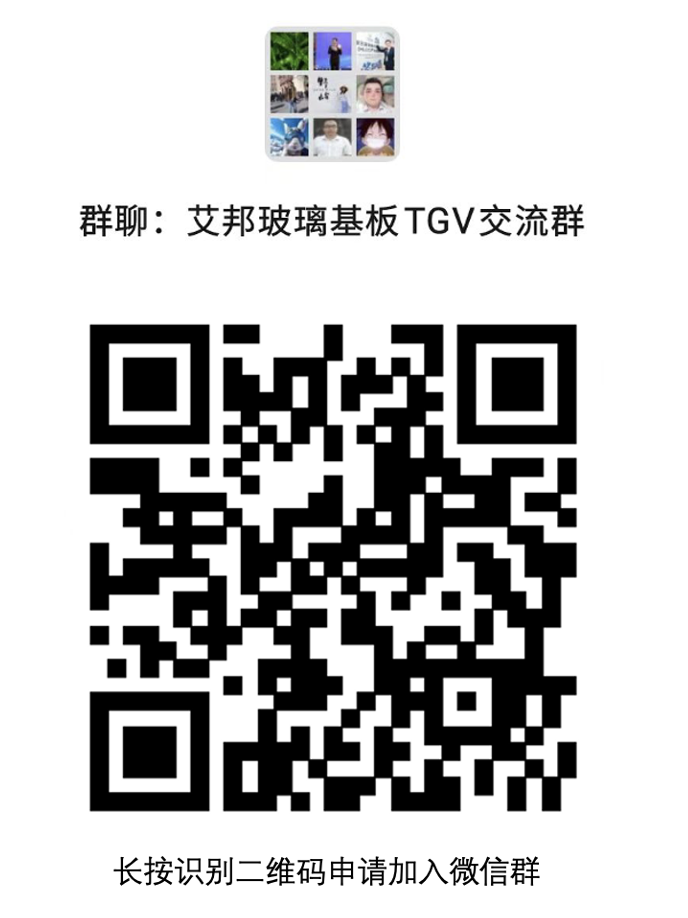